深圳专业磁控溅射优点
真空磁控溅射镀膜技术所镀玻璃多用于建筑玻璃和汽车玻璃这两大用处。一般来说这些介质膜多是氧化锌、二氧化锡、二氧化钛、二氧化硅之类的可镀于玻璃上。真空磁控溅射镀膜技术在车窗玻璃上的用处。用真空磁控溅射镀膜设备可在车窗玻璃镀涂二氧化钛,这个镀层可以赋予车窗自清洁效果,有一定的防雾、防露水的效用。磁控溅射工艺的主要优点是可以使用反应性或非反应性镀膜工艺来沉积这些材料的膜层,并且可以很好地控制膜层成分、膜厚、膜厚均匀性和膜层机械性能等。真空磁控溅射镀膜特别适用于反应沉积镀膜。深圳专业磁控溅射优点
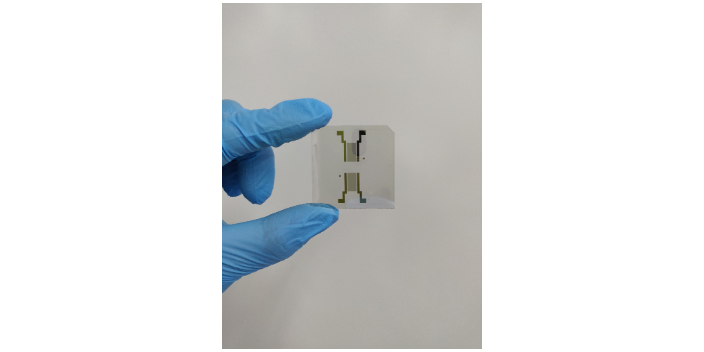
磁控溅射的基本原理是利用Ar一O2混合气体中的等离子体在电场和交变磁场的作用下,被加速的高能粒子轰击靶材表面,能量交换后,靶材表面的原子脱离原晶格而逸出,转移到基体表面而成膜。磁控溅射的特点是成膜速率高,基片温度低,膜的粘附性好,可实现大面积镀膜。该技术可以分为直流磁控溅射法和射频磁控溅射法。磁控溅射设备一般根据所采用的电源的不同又可分为直流溅射和射频溅射两种。直流磁控溅射的特点是在阳极基片和阴极靶之间加一个直流电压,阳离子在电场的作用下轰击靶材,它的溅射速率一般都比较大。但是直流溅射一般只能用于金属靶材,因为如果是绝缘体靶材,则由于阳粒子在靶表面积累,造成所谓的“靶中毒”,溅射率越来越低。深圳多层磁控溅射方案这提高了薄膜工艺的效率,使它们能够在较低的压力下更快地生长。
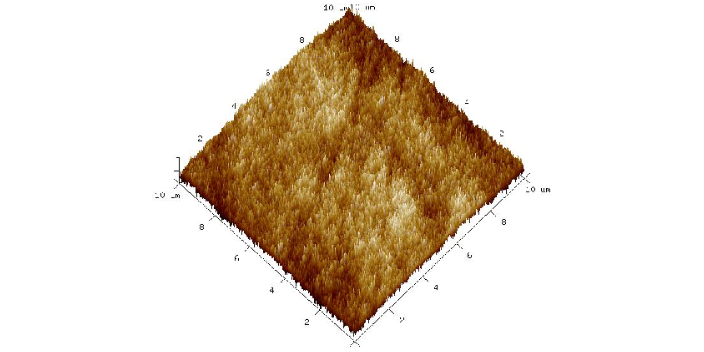
磁控溅射镀膜注意事项:1、辐射:有些镀膜要用到射频电源,如功率大,需做好屏蔽处理.另外,欧洲标准在单室镀膜机门框四周嵌装金属线屏蔽辐射;2、金属污染:镀膜材料有些(如铬、铟、铝)是对人体有害的,特别要注意真空室清理过程中出现的粉尘污染;3、噪音污染:如特别是一些大的镀膜设备,机械真空泵噪音很大,可以把泵隔离在墙外;4、光污染:离子镀膜过程中,气体电离发出强光,不宜透过观察窗久看.磁控溅射镀膜的产品特点。磁控溅射镀膜的适用范围:1、建材及民用工业中;2、在铝合金制品装饰中的应用;3、高级产品零/部件表面的装饰镀中的应用;4、在不锈钢刀片涂层技术中的应用;5、在玻璃深加工产业中的应用。
磁控溅射技术不只是科学研究和精密电子制造中常用的薄膜制备工艺技术,经过多年的不断完善和发展,该技术也已经成为重要的工业化大面积真空镀膜技术之一,普遍应用于玻璃、汽车、医疗卫生、电子工业等工业和民生领域。例如,采用磁控溅射工艺生产镀膜玻璃,其膜层可以由多层金属或金属氧化物祖成,允许任意调节能量通过率、反射率,具有良好的美观效果,被越来越多的被应用于现代建筑领域。再比如,磁控溅射技术也能够应用于织物涂层,这些织物涂层可以应用于安全领域,如防电击、电磁屏蔽和机器人防护面料等,也可用于染料制作。这样的涂层织物在医疗卫生、环境保护、电子工业等领域都有重要的应用。PVD镀膜技术主要分为三类:真空蒸发镀膜、真空溅射镀膜和真空离子镀膜。
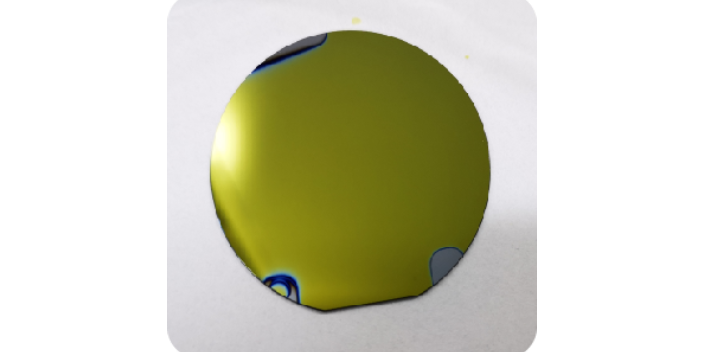
真空磁控溅射的分类:平面磁控溅射:平衡平面溅射是较常用的平面靶磁控溅射,磁力线有闭合回路且与阴极平行,即在阴极表面构成一个正交的电磁场环形区域。等离子体被束缚在靶表面距离靶面大约60cm的区域,通常在基片上加负偏压来改善膜与基体的结合能力;非平衡平面磁控溅射为了将等离子区域扩展,利用磁体摆放方式的调整,可以方便的获得不同的非平衡磁控源。圆柱磁控溅射沉积技术:利用圆柱形磁控阴极实现溅射的技术磁控源是关键部分,阴极在中心位置的叫磁控源;阳极在中心位置的叫反磁控源。磁控溅射在技术上可以分为直流(DC)磁控溅射、中频(MF)磁控溅射、射频(RF)磁控溅射。四川磁控溅射优点
磁控溅射就是以磁场束缚和延长电子的运动路径,改变电子的运动方向。深圳专业磁控溅射优点
脉冲磁控溅射的分类:(1)单向脉冲:单向脉冲正电压段的电压为零!溅射发生在负电压段。由于零电压段靶表面电荷中和效果不明显。(2)、双向脉冲:双向脉冲在一个周期内存在正电压和负电压两个阶段,在负电压段,电源工作于靶材的溅射,正电压段,引入电子中和靶面累积的正电荷,并使表面清洁,裸露出金属表面。双向脉冲更多地用于双靶闭合式非平衡磁控溅射系统,系统中的两个磁控靶连接在同一脉冲电源上,两个靶交替充当阴极和阳极。阴极靶在溅射的同时,阳极靶完成表面清洁,如此周期性地变换磁控靶极性,就产生了“自清洁”效应。深圳专业磁控溅射优点
广东省科学院半导体研究所是一家有着雄厚实力背景、信誉可靠、励精图治、展望未来、有梦想有目标,有组织有体系的公司,坚持于带领员工在未来的道路上大放光明,携手共画蓝图,在广东省等地区的电子元器件行业中积累了大批忠诚的客户粉丝源,也收获了良好的用户口碑,为公司的发展奠定的良好的行业基础,也希望未来公司能成为*****,努力为行业领域的发展奉献出自己的一份力量,我们相信精益求精的工作态度和不断的完善创新理念以及自强不息,斗志昂扬的的企业精神将**广东省科学院半导体研究所供应和您一起携手步入辉煌,共创佳绩,一直以来,公司贯彻执行科学管理、创新发展、诚实守信的方针,员工精诚努力,协同奋取,以品质、服务来赢得市场,我们一直在路上!
上一篇: 河南半导体器件加工平台
下一篇: 浙江射频磁控溅射流程