北京精密塑料模具定做厂家
塑料模具的数控加工具有一定典型性,并比普通产品的数控加工有更高的要求。在模具的加工中,各种数控加工均有用到,使用较多的是数控铣及加工中心,数控线切割加工与数控电火花加工在模具数控加工中的使用也十分遍及,线切割首要使用在各种直壁的模具加工,如冲压加工中的凹凸模,吹塑模中的镶块、滑块,电火花加工用的电极等。关于硬度比较高的模具零件,选用机加工办法无法加工,大多选用电火花加工,另外关于模具型腔的尖角、深腔部位、窄槽等也使用电火花加工。而数控车床首要用于加工模具杆类标准件,以及回转体的模具型腔或型芯,如瓶体、盆类的吹塑模具,轴类、盘类零件的锻模。在模具加工中,数控钻床的使用也可以起到提高加工精度和缩短加工周期的作用。模具安装后预热的一起,打针机筒也在加温,当两者温度均符合要求时,即模具温度达30〜60℃以上时。北京精密塑料模具定做厂家
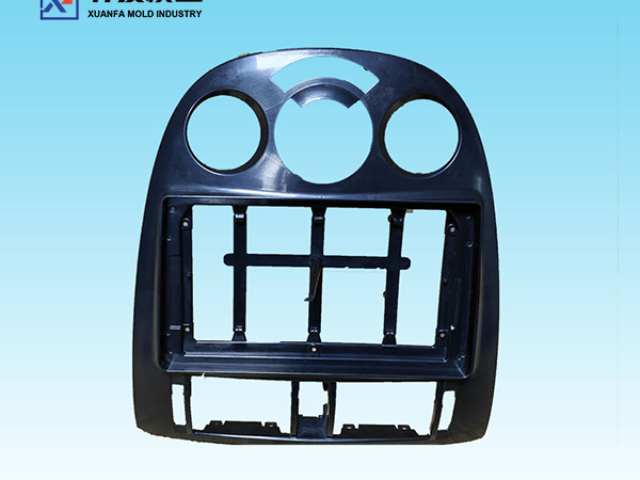
塑料模具是生产各种工业产品的重要工艺装备,随着塑料工业的迅速发展,以及塑料制品在航空、航天、电子、机械、船只和轿车等工业部门的推广使用,产品对模具的要求也越来越高,传统的模具设计办法已无法适应当今的要求。与传统的塑料模具设计比较,计算机辅助工程(CAE)技能无论是在提高生产率、保证产品质量方面,仍是在降低成本、减轻劳动强度方面,都具有极大的优越性。如何去提高塑料模具的加工功能:一、多种测量技能的复合应用、高速测量及其逆向工程将成为推动塑料模具开发以及规划技能的发展方向。二、塑料模具加工的模具钢资料硬度高,这就要求塑料模具这类加工设备要具有热稳定性、高可靠性。三、加工技能与绿色产品技能的结合将在企业采购设备时纳入考虑范围。上海花盆塑胶模具多少钱塑料模具特点:选用龙记标准模架。
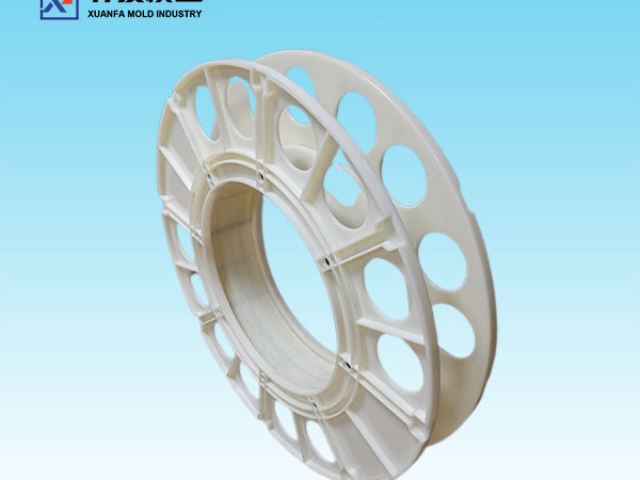
决定模具使用寿命比较重要的因素往往是模具材料的耐磨性。模具在工作中接受相当大的压应力和摩擦力,要求模具可以在激烈摩擦下仍保持其尺度精度。模具的磨损主要是机械磨损、氧化磨损和熔融磨损三种类型。为了改善模具钢的耐磨性,就要既保持模具钢具有高的硬度,又要确保钢中碳化物或其他硬化相的组成、描摹和散布比较合理。对于重载、高速磨损条件下执役的模具,要求模具钢表面能形成薄而致密粘附性好的氧化膜,保持润滑作用,削减模具和工件之间产生粘咬、焊合等熔融磨损,又能削减模具表面进行氧化造成氧化磨损。所以模具的工作条件对钢的磨损有较大的影响。耐磨性可用模拟的实验方法,测出相对的耐磨指数,作为表征不同化学成分及安排状态下的耐磨性水平的参数。以出现规则毛刺高度前的寿命,反映各种钢种的耐磨水平;实验是以钢为基准进行比照。
塑料模具生锈的原因:1、熔料过热分解后,产生气体造成的。如果发生在暂停成型时,塑料模具周围存在的腐蚀性气体是会把模具锈蚀的。因此,在长时间停止成型时,应在模腔内喷射防锈剂等。2、模腔内的电镀层虽有利于防锈,但是并不完全有效。有时,腐蚀性气体会通过镀层表面的气孔产生深度腐蚀;因此,避免镀层锈蚀的方法是勤擦塑料模具。3、模具中通冷却水易使塑料模具生锈。如将模具冷却到零点以下,空气中的潮气就会在模具表面结成水珠,如不擦除就会生锈。塑料模具也是很容易生锈的。
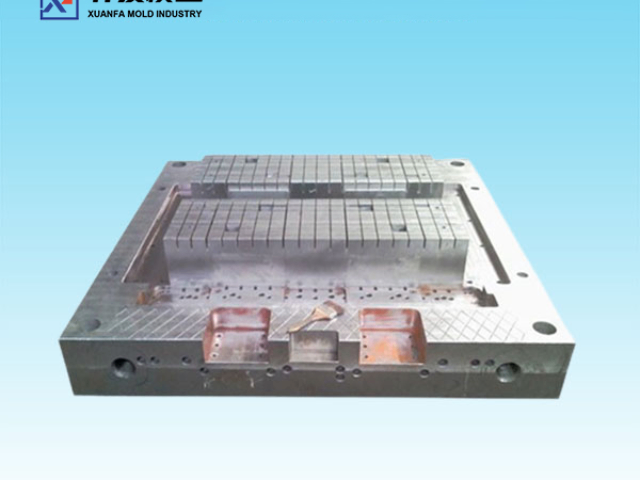
大型塑料模具主要用于生产体积庞大的塑料制品,如储水罐、游泳池、大型容器等。这些模具不只尺寸巨大,还要求具有出色的结构强度和稳定性,以确保在注塑过程中能够承受高压和高温。在农业、建筑和化工等行业,大型塑料模具生产的制品因其成本低、重量轻、耐腐蚀等优点而备受青睐。随着技术的进步,大型模具的制造周期不断缩短,生产效率卓著提升,为相关行业带来了更多的发展机遇。UG作为一款强大的CAD/CAM/CAE软件,在塑料模具设计与制造领域发挥着重要作用。它提供了从产品设计到模具制造的一站式解决方案,支持复杂曲面的建模、模具分型面的设计、模流分析等关键步骤。通过UG,工程师可以更加高效地创建和优化模具结构,减少试模次数,缩短产品开发周期。此外,UG还支持与数控机床的无缝对接,实现模具的精确加工和高效生产。塑料模具加工的模具钢资料硬度高,这就要求塑料模具这类加工设备要具有热稳定性、高可靠性。南京汽车塑胶模具结构
塑料模具目前的应用是较为普遍的。北京精密塑料模具定做厂家
在确保证塑料模具硬度的前提下,尽量选用预冷、分级冷却淬火或温淬火工艺。常平热处理建议。对精细杂乱模具,在条件许可的情况下,氮化热处理厂建议尽量选用真空加热淬火和淬火后的深冷处理。对一些精细杂乱的模具可选用预先热处理、时效热处理、调质氮化热处理来操控模具的精度。氮化热处理厂在修补模具砂眼、气孔、磨损等缺陷时,选用冷焊机等热影响小的修复设备以避免修补过程中变形的发生。模具结构设计要合理,厚薄不要太悬殊,形状要对称,行家表明,对于变形较大模具要把握变形规则,预留加工余量,对于大型、精细杂乱模具可选用组合结构。精细杂乱模具要进行预先软氮化,消除机械加工过程中发生的残余应力。北京精密塑料模具定做厂家
上一篇: 武汉包胶折叠注塑模具制作
下一篇: 深圳外壳注塑模具公司