注射器雾化喷涂供应商
雾化喷涂是一种常用的表面处理技术,可以为产品提供耐化学品腐蚀的保护层,延长产品使用寿命。这种技术的耐腐蚀性能取决于喷涂材料的化学成分和结构。通常情况下,雾化喷涂所使用的材料都具有较高的化学稳定性和抗腐蚀性能,能够有效地防止化学物质对产品表面的侵蚀和损伤。此外,雾化喷涂还可以通过改变喷涂材料的成分和结构来提高其耐腐蚀性能,使其适用于更加恶劣的环境条件下的使用。在工程领域中,雾化喷涂被普遍应用于各种金属和非金属材料的表面处理和保护。其主要作用是形成一层均匀、致密、具有较高硬度和耐磨性的保护层,有效地防止产品表面的磨损和腐蚀。雾化喷涂液体通过喷头导入到雾化面。注射器雾化喷涂供应商
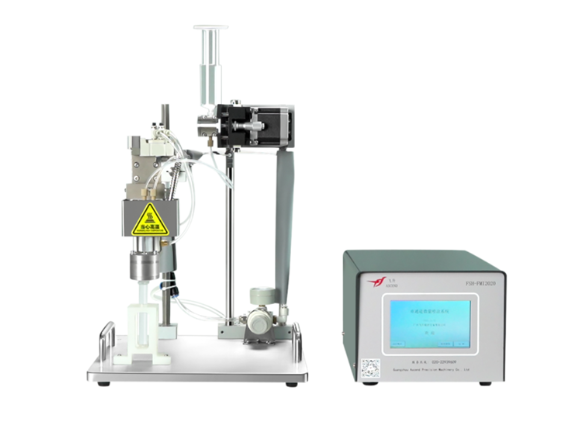
雾化喷涂如何应用于点胶行业?1、胶液接触转轮,易污染机器,不易清洗。2、胶液转涂不均匀,胶量不易控制。3、涂胶过程麻烦,调试不方便。而雾化喷涂由于输送时只接触泵管,可以连续并精确的将粘胶输送到制定位置,因此可以解决合掌机用涂胶时存在的问题。胶液的粘性非常高,不同于一般的水性流体,因此能保证高效长期稳定的涂胶,雾化喷涂应用于合掌机中的注意事项:1、选择泵管时要采用壁厚稍厚的雾化喷涂软管。2、适当采用内口径稍大的雾化喷涂软管。3、尽可能的降低雾化喷涂的转速,通常转速控制在50rpm以内。4、要定期检查并提前更换泵管,防止泵管破裂。5、在选择雾化喷涂的时候要尽量选择可以耐胶耐腐蚀结构强度好的雾化喷涂泵头,驱动器选择方面较好选择具有流量显示功能和校正功能的雾化喷涂。注射器雾化喷涂供应商雾化喷涂使用高性能的钛合金及不锈钢制造。
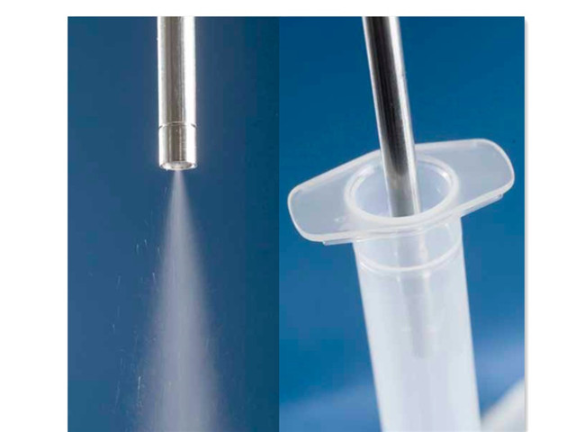
雾化喷涂可以提高产品的表面质量和光洁度,使其具有更好的外观和触感。在工程实践中,雾化喷涂已经成为一种重要的表面处理技术,为各种产品的生产和使用提供了可靠的保护。雾化喷涂不仅可以为产品提供耐化学品腐蚀的保护层,延长产品使用寿命,还可以节约能源和降低生产成本。相比于传统的表面处理技术,雾化喷涂具有更高的效率和更低的能耗,可以在短时间内完成大量的喷涂作业。此外,雾化喷涂还可以减少废料和污染物的产生,降低环境污染和治理成本。因此,雾化喷涂不仅具有良好的保护效果,还可以为企业带来明显的经济效益和社会效益。
雾化喷涂是一种常用的表面涂装技术,可以在不同的材料表面上形成均匀、光滑、耐磨的涂层。然而,不同的材料对雾化喷涂的影响是不同的。首先,材料的表面粗糙度和化学成分会影响涂层的附着力和耐久性。其次,材料的热膨胀系数和热导率会影响涂层的热稳定性和导热性能。因此,在选择雾化喷涂材料时,需要考虑材料的表面质量、化学成分、热性能等因素,以确保涂层的质量和性能。例如,在汽车制造中,常用的雾化喷涂材料包括钢铁、铝合金、塑料等。钢铁具有强度高和耐腐蚀性,但表面粗糙度较高,需要进行表面处理以提高涂层的附着力。铝合金具有轻质、强度高和良好的导热性能,但易受氧化影响,需要进行表面处理以提高涂层的耐久性。塑料具有轻质、耐腐蚀和绝缘性能,但表面粗糙度较低,需要进行表面处理以提高涂层的附着力。因此,在选择雾化喷涂材料时,需要根据具体应用场景和要求,综合考虑材料的表面质量、化学成分、热性能等因素,以选择合适的材料。雾化喷涂需要严格按照规范。
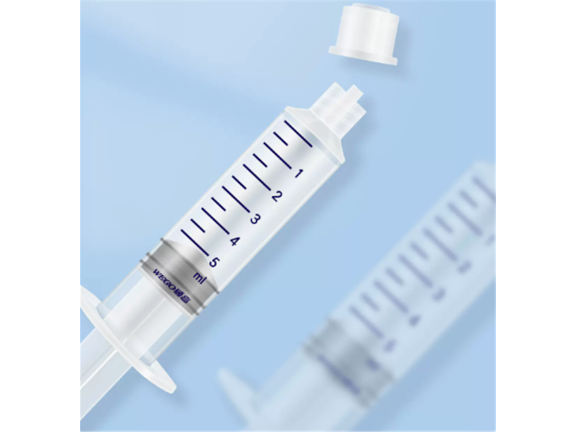
雾化喷涂技术是一种高效、准确的涂装技术,可以为产品提供耐用的外观涂层,从而增加产品的市场吸引力。在现代工业生产中,产品的耐用性是消费者非常关注的一个方面,因为耐用的产品可以为消费者节省更多的成本和时间。雾化喷涂技术可以通过选择不同的涂料和涂层厚度,实现不同的耐用性要求,如耐磨、耐腐蚀、耐高温等。此外,雾化喷涂技术还可以实现特殊的涂层效果,如防水、防尘、防紫外线等,从而增加产品的使用寿命。因此,雾化喷涂技术是一种非常重要的涂装技术,可以为产品提供耐用的外观涂层,从而增加产品的市场吸引力。雾化喷涂利用加温氮气替代传统的压缩空气进行喷涂。广东硅油雾化喷涂系统
雾化喷涂是利用超声波能量使液体在气相中形成微细雾滴的过程,。注射器雾化喷涂供应商
雾化喷涂静电场雾化。传统的空气油漆雾化器主要使用空气动力学的气压来喷涂油漆,然后用空气油漆雾化器将雾化粒子喷涂到车身上。因此,油漆颗粒会被空气从车身上喷散开来,导致涂层效率较低。因此诞生了低空气流量技术、静电和旋杯辅助传输等技术,且得到推广应用体现了很好的节约涂料效果。喷漆利用率提升的高境界彻底取消空气雾化,涂料靠静电场自然吸附到产品之上,汽车去年就发布了这样一种汽车烤漆雾化设备。新型无气式喷漆雾化器使用静电喷涂油漆(静电雾化),而这种静电带粒子涂层的方式利用重力使漆烤附在车身上(静电喷涂)。静电雾化和静电喷涂技术很大方面减少了散射的雾化颗粒数量,实现超过95%的喷涂效率,目前该装备已经进入实用阶段。大量部署的话集团可将二氧化碳排放量减少大约7%,单车油漆用量和VOC排放都将减少,喷涂烤漆产线的运行成本大量降低。注射器雾化喷涂供应商
上一篇: 北京预充式雾化喷涂公司
下一篇: 重庆冻干微球分装机