换挡冲击小35吨地下运矿车动力换挡变速箱
动力换挡变速箱的结构:实现动力换挡的主要控制元件有动力换挡变速箱、拖拉机电液控制单元、液压系统三大部分。变速箱的液压控制系统除对变速箱强制润滑外,还控制换挡离合器、主离合器、PTO和前桥驱动的分离和结合,以及制动器的制动。变速箱的主要性能参数,包括发动机输入转速、变速箱输入转速、液力变速箱输出转速、主离合器转速、离合器踏板位置、离合器位置、主变速箱挡位、PTO转速、变速箱温度、润滑系统油压等,通过各类传感器传递至变速箱电子控制单元(TCU),TCU根据驾驶员输入指令,控制液压系统中的电磁阀和对应的换挡离合器实现换挡,同时对转速、转矩、压力、流量、温度等进行监测。开发动力换挡变速箱,均需对(TCU)进行开发和参数设定,保证其控制的稳定和一致性。动力换挡技术其实就是变速箱在换挡的瞬间,动力不终端的换挡技术。换挡冲击小35吨地下运矿车动力换挡变速箱
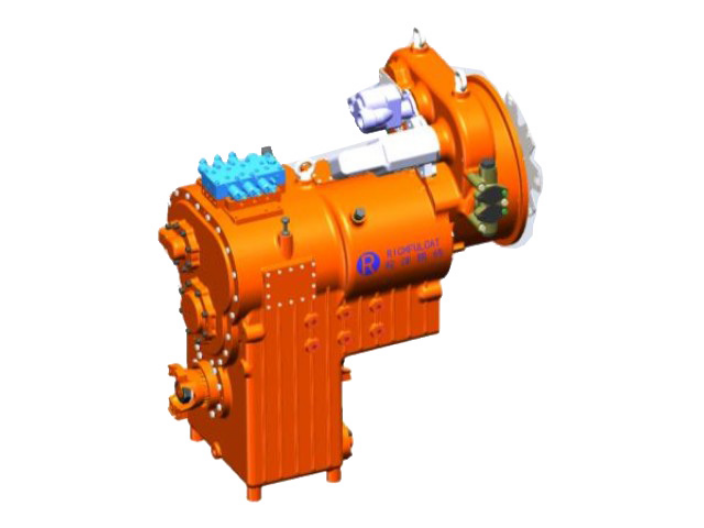
动力换挡变速箱改变传动比,满足不同行驶条件对牵引力的需要,使发动机尽量工作在有利的工况下,满足可能的行驶速度要求。在较大范围内改变汽车行驶速度的大小和汽车驱动轮上扭矩的大小。由于汽车行驶条件不同,要求汽车行驶速度和驱动扭矩能在很大范围内变化。例如,在高速路上车速应能达到100km/h,而在市区内,车速常在50km/h左右。空车在平直的公路上行驶时,行驶阻力很小,则当满载上坡时,行驶阻力便很大。而汽车发动机的特性是转速变化范围较小,而转矩变化范围更不能满足实际路况需要。国产的6立方地下铲运车动力换挡变速箱动力换挡变速箱由变速传动机构和变速操纵机构两部分组成。
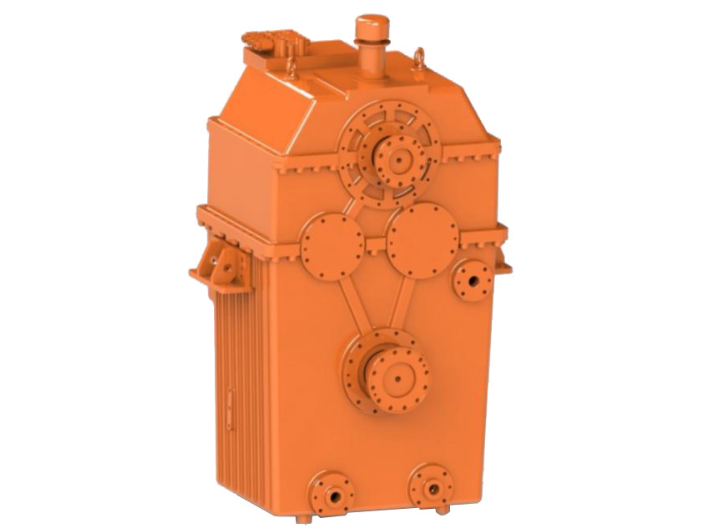
简单来说动力换挡变速箱就是换挡过程中动力不中断的技术,一般来说通常我们所见到的变速箱在换挡的时候,首先需要完全踩下离合器,然后拨动换挡杆,将变速箱切换到自己的目标档位,然后松开离合器,加油,从而完成整个换挡过程。在这一过程中明显可以看到动力是中断了的换挡,这种模式在公路用车上没有什么问题,但是对于重载的拖拉机,尤其是在耕地的过程中存在明显的劣势,动力中断之后再重新结合,对发动机来说,巨大的负载变化严重影响到发动机工作的平顺性和使用寿命。所以自动力换挡变速箱在大马力拖拉机上应用以来,在欧美等农机产业发达的国家得到了大范围的应用和推广。动力换挡变速箱(英文:Transmission),又称变速箱,是用来改变来自发动机的转速和转矩的机构,它能固定或分档改变输出轴和输入轴传动比。动力换挡变速箱由变速传动机构和操纵机构组成,有些汽车还有动力输出机构。传动机构大多用普通齿轮传动,也有的用行星齿轮传动。
动力换挡变速箱的应用现状功率范围:73.5kW(100hp)以上。带有动力换向的动力换挡传动系是应用的主流,具有较好的性价比,应用功率范围逐渐加大。部分动力换挡传动系应用范围已扩展到了73.5kW功率段,随着液压元件性能的提升和计算机控制技术的应用,动力换挡和动力换向技术从依靠液压反馈控制换挡过程,发展为采用传动系电控系统(TCU)控制换挡过程。TCU根据换挡时负荷、转速、油温、油压等数据对换挡过程自动实时控制。还可实现与其他部件的综合自动控制,进一步提高操纵舒适性和工作效率。全动力换挡传动系由于结构复杂、成本高,正逐步退出大功率段,主要应用在147kW(200hp)以上的大功率段拖拉机产品,以发挥其传动效率高的特点。随着液压元件性能的提升,液压传动效率有了明显改善,液压机械双流传动的CVT传动系得到了更为普遍的采用。动力换挡变速箱主要应用了齿轮传动的降速原理。
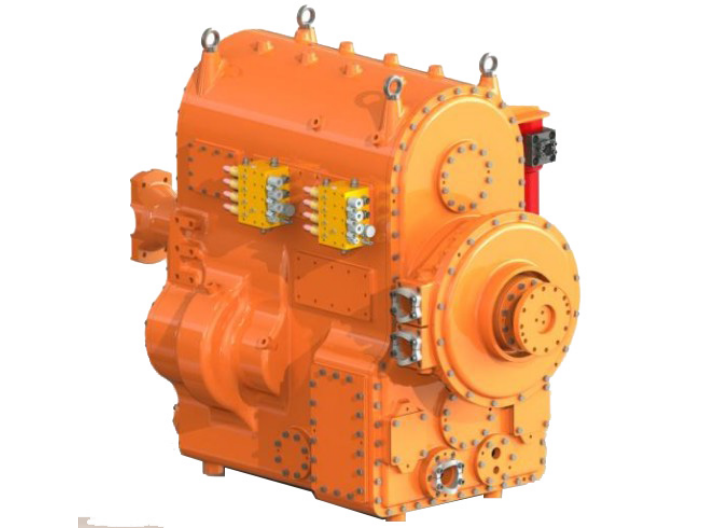
为了提高发动机的利用功率,现代设备上,2~4挡的动力换挡变速箱与机械换挡变速箱组成部分动力换挡变速箱。其中,两挡动力换挡由于结构较简单、造价较低,已获得宽泛采用。由多个行星机构串联成全动力换挡变速箱,其操作方便,可获得较高的生产率,只在部分大功率拖拉机上采用。两挡动力换挡用于部分动力换挡的变速箱中,可实现高低挡间不停车换挡。当负载增大时换入低挡,负载减小则换入高挡。这样,能使有级变速箱增加一倍的排挡数。内啮合行星式动力换挡机构如图所示动力换挡就是通过湿式离合器控制变速箱换挡,通过液压控制系统实现传动器的不间断换挡、换向操作。动力换挡技术是相对于传统的机械换挡而言的。动力换挡拖拉机采用电子控制系统,实现了拖拉机不间断换挡、换向,将复杂的操作过程简化为简单的按钮操作,驾驶员可以在极其短暂的时间内轻松完成复杂的各种作业过程,不只降低了操作难度和劳动强度,而且还提高了作业质量,从而实现了作业效率的提升。动力换挡变速箱十二个月或两万公里更换一次动力换挡变速箱油。湖南65吨隧道机车动力换挡变速箱
一般建议动力换挡变速箱油2年或者4万公里更换。换挡冲击小35吨地下运矿车动力换挡变速箱
动力换挡变速箱齿轮经常处在不断变化的转速,负荷下进行工作,齿轮齿面又受到冲击载荷的冲击,致使齿轮(特别是齿面)产生损伤.常见损伤有:(1)齿轮磨损动力换挡变速箱齿轮在正常工作条件下,齿面呈现出均匀的磨损,要求沿齿长方向磨损不应超过原齿长的百分之30;齿厚不应超过0.40;齿轮啮合面积不低于齿面的3分之2;运转齿轮啮合间隙一般应为0.15-0.26mm,使用限度为0.80mm;接合齿轮啮合间隙应为0.10-0.15mm,使用限度为0.60mm。可用百分表或软金属倾轧法测量。如果超过间隙,应成对更换。(2)齿轮轮齿破碎轮齿破碎,主要是由于齿轮啮合间隙不符合要求,轮齿啮合部位不当或工作中受到较大的冲击载荷所致。若轮齿边缘有不大于2mm的微小破碎,可用油石修磨后继续使用;若超过这个范围或有3处以上微小破碎,则应成对更换。(3)常啮合齿轮端面磨损常啮合的斜齿端面应有0.10-0.30mm的轴向间隙,以保证齿轮良好运转,若齿端磨损起槽,可磨削修复,但磨削量应不超过0.50mm。换挡冲击小35吨地下运矿车动力换挡变速箱
上一篇: 广东25吨隧道机车传动系统
下一篇: 哈尔滨8立方 地下铲运车传动系统