北京快速成型铸件制造
压铸件:压铸工艺将熔融金属在高压下压入模具型腔(将其加工成模具)。大多数压铸件都由有色金属制成,特别是锌、铜和铝基合金,但是黑色金属压铸件也是可行的。压铸法特别适用于需要许多中小型零件且具有良好的细节,良好的表面质量和尺寸一致性的应用。半固态金属(SSM)铸造是一种改进的压铸工艺,可减少或消除大多数压铸件中存在的残留孔隙率。SSM铸造不使用液态金属作为进料,而是使用部分固体和部分液体的高粘度进料。使用改进的压铸机将半固态浆料注入可重复使用的硬化钢模中。半固态金属的高粘度以及受控模头填充条件的使用确保了半固态金属以非湍流的方式填充模头,从而可以基本上消除有害的气孔。金属铸件,就选无锡协铸智能制造有限公司,让您满意,欢迎新老客户来电!北京快速成型铸件制造
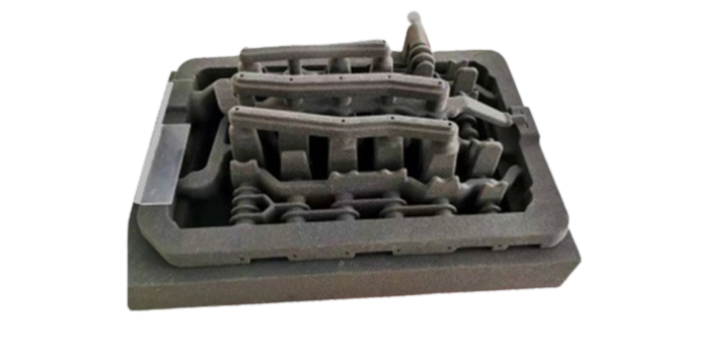
导致铸造件碳含量超标准的缘故关键有几个方面:1,铸件的模样材料选择不合理。在铸件白模模样材料的选择中,一是含碳量高;二是白模密度太高。从而造成铸件模样在浇注过程中的热分解时含碳量高,使铸件在浇注充型过程中液相及雾状游离碳含量高,造成铸钢件的渗碳机率增大。2,铸钢件的生产熔炼配料中碳含量未严格控制,特别是各种废钢中的含碳量和各种废钢中是否存在有其他合金成分的材料不明。3,铸件的模样组合粘接面多。模样组合件质量差、组合面不光滑平整,造成模样在组合粘接时用胶量增大,则其热分解产物的含碳量增高。福建铜铸件制造金属铸件,就选无锡协铸智能制造有限公司,有需要可以联系我司哦!
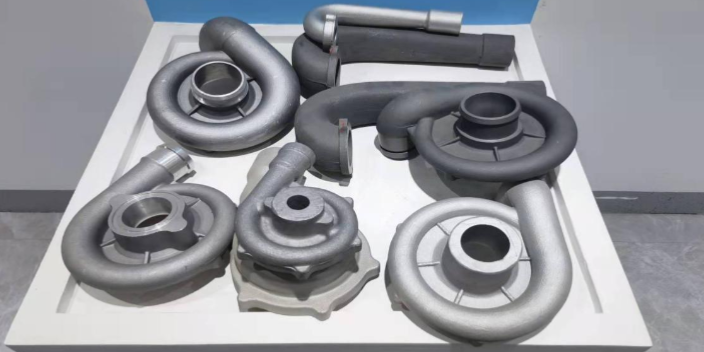
铝合金简单吸气和氧化,所以浇注体系确保铝液流入快速安稳,避免搅拌。各种铸造办法适用于压铸件。当产值较低时,能够使用砂型铸造,应选择细砂进行造型;关于大量生产的重要压铸件,选用特别铸造。金属铸造效率高,压铸件质量好,低压铸造适用于要求高细密性的耐水压铸件,压力铸造可用于薄壁复杂的小零件。铸造铝材成本低,工艺性好,再熔节约资源和动力,因而该资料的使用和开展是的。例如,研讨冲天炉-电炉双联熔炼技能和设备***选用铁液脱硫、过滤技能薄壁铸铁资料制作技能铸铁复合资料制作技能铸铁资料外表或局部强化技能等温磷寸球墨铸铁成套技能选用金属型铸造和金属型覆砂铸造、接连铸造等特别技能和设备等。铸造铝轻合金因其密度小、比强度高、耐腐蚀等一系列优良特性,将在航空、航天、轿车、机械等职业得到很普遍的使用。特别是在轿车工业,为了降低油耗,提高动力利用率,用铝和镍合金压铸件替代钢和铁压铸件是一个长期的开展趋势。
铸件在生产过程中,由于多种因素影响,常常会出现气孔、夹渣、裂纹、凹坑等缺陷。这时候为了使铸件能够达到使用标准,减少损失浪费,往往会对缺陷进行修复。常用的修补设备为氩弧焊机、电阻焊机、冷焊机等。对于质量与外观要求不高的铸件缺陷可以用氩弧焊机等发热量大、速度快的焊机来修补。但在精密铸件缺陷修补领域,由于氩焊热影响大,修补时会造成铸件变形、硬度降低、砂眼、局部退火、开裂、磨损、划伤、咬边、或者是结合力不够及内应力损伤等二次缺陷。冷焊机正好克服了以上缺点,其优点主要表现在热影响区域小,铸件无需预热,常温冷焊修补,因而无变形、咬边和残余应力,不会产生局部退火,不改变铸件的金属组织状态。无锡协铸智能制造有限公司为您提供专业的金属铸件,有想法的可以来电咨询!
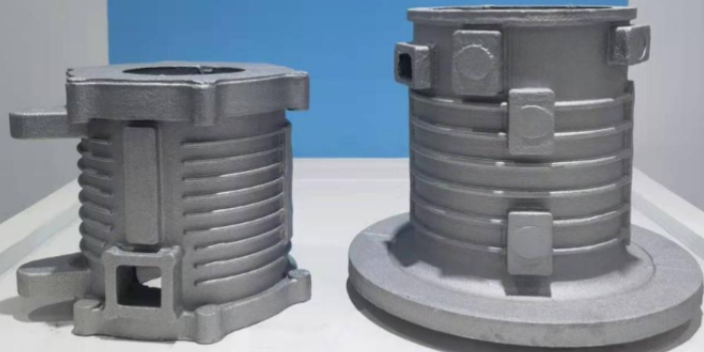
不锈钢铸件在调质处理后的铸造件必须合理的开展检测其物理性能,铸造件中氩弧焊机区总面积干万不可以低于2cm2,机器设备焊区间隔不经济效益100毫米,在运用时并不通过其热处理工艺,可是一处不锈钢铸件上干万不可以超过5处。不锈钢精密铸造件在开展焊补区是不可有裂痕及其未满焊的状况的,铸造件在一切一焊区中是容许有较大直徑不得超过2毫米且不可以超出壁厚的1/3的出气孔或参杂三种,商品的行高不经济效益12毫米。不锈钢铸件在浸蚀物质及其氛围中运行的铸造件,商品在焊伤停补时是不允许应用焊粉,从容许规定对钙化性的不锈钢铸件开展渗补解决。金属铸件,就选无锡协铸智能制造有限公司,欢迎客户来电!安徽铁铸件哪家好
金属铸件,就选无锡协铸智能制造有限公司,用户的信赖之选。北京快速成型铸件制造
我们在日常应用铝铸件的历程中,一定要按时的对其进行适度的保养,不可以等其发生裂痕等别的欠佳以后才对你开展保养工作中,因此当铝铸件发生裂痕以后在对其保养得话,毫无疑问会对铝铸件的使用期限减少许多,因此大伙儿一定要记牢铝铸件的按时保养十分关键。实际上铝铸件在保养以前,务必先对其进行打磨抛光和抛光,由于只能如此能够高效的做到保养的实际效果,长期性的应用铝铸件得话,铝铸件的表层一定会产生许多微小的裂痕,而这种裂痕假如不可以获得及早高效的解决得话,那么铝铸件会很容易发生破裂的状况。假如大伙儿针对铝铸件在保养上也有其他疑惑得话,均可打电话我企业开展深入分析。北京快速成型铸件制造