杭州单片式改装车轮毂按需定制
旋压与低压铸造的区别:
1、低压铸造是将金属液体通过设备施加压力灌注到铸模之中,在这个过程中一直保持一个恒定压力,在保证了金属液体的密度同时,也保证了凝固后金属的强度。并且低压铸造的过程全部由机械完成,并且铸造成型的良品率高,非常适合大批量生产,所以目前汽车厂商指定的铸造铝合金轮毂都是由这种工艺生产出来的。
旋压铸造技术则是在铸造技术上演变而来,在铸造后的毛坯轮毂进行在加工处理,主要是对轮辋部分行旋转冲压,这个过程中轮辋部分被加热同时旋刀进行旋转,将轮辋逐渐拉长变薄。此时轮辋内部金属分子排列更为紧密,所以此处的金属强度更高。
旋压轮毂是怎么发展起来的?杭州单片式改装车轮毂按需定制

轮毂轮辐镂空设计的原因?(二)
3. 镂空设计能节约原材料:镂空设计节省了轮毂制造所用的铝合金、镁合金等原材料,降低了轮毂生产厂家的生产成本,进而降低了主机厂的成本,消费者也享受到了实惠。
4、镂空设计的轮毂更美观:当今社会是个论颜值的时代,汽车轮毂也是一样。目前汽车厂家也越来越重视轮毂的轮辐造型设计,好的轮毂设计可以增强整车造型的设计完整性,起到画龙点睛的作用。 镂空的辐条还能做出各式各样的造型,满足不同消费者的需求。
杭州镁合金改装车轮毂定做价格轮毂上的小铁块有什么作用?

为什么有的轮毂上有一个或几个大小不等的小铁块?汽车的车轮是由轮胎、轮毂组成的一个整体。 但由于制造商的原因,车轮各部分的重量分布不可能是非常均匀的。当车轮高速旋转起来时,就会形成动不平衡的状态,造成车辆的行驶不稳定、方向盘振动等现象。为了避免这种现象或是消除已经发生的这种现象,就要使车轮在动态情况下通过增加配重的方法,校正车轮各边缘部分的平衡。这个校正的过程就是人们常说的动平衡,校正使用的就是小铁块。别小看了车轮的动平衡,也别小瞧了那一块块不起眼的小铅块,如果车轮动平衡不好会造成轮胎的异常磨损,也会影响车辆的稳定性。
与低压铸造轮毂相比,旋压轮毂的轮圈部分用旋压机通过强 力旋压,分子密度得到提 升,轮圈具有强刚性。因此,旋压轮毂比铸造轮毂坚 固耐 用,安 全性也高很 多。此外,旋压轮毂的重量也比铸造轮毂轻,轮毂的操作性更灵活,也更节能。从外观上看,铸造轮毂因为是由铝液倒入模具制成,在凝固脱模时,容易在轮毂条幅侧面产生拔模角度。而尚晞旋压轮毂是先锻后旋,不存在拔模角度,辐条更细且轮廓分明,美观度大幅提 升。目前很多车主在改装自己爱车时都选择了旋压轮毂。 怎样才能识别旋压轮毂?
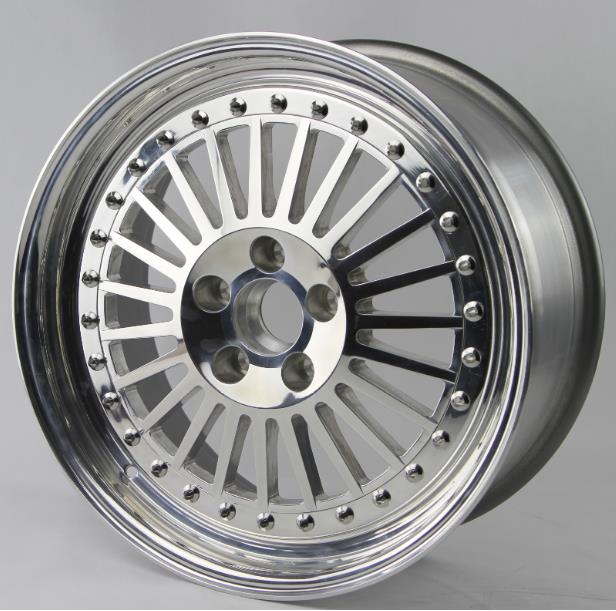
旋压轮毂的工艺发展路程。铝合金轮毂旋压成形是在铝合金热锻工艺基础上发展起来的,锻造制坯后进行旋压成形,提高了制造精度和强度,机械加工余量**减少。旋压轮毂产品美观、性能良好、安全性高、节省材料、节约能源等因素,获得了市场的认可,发展势头良好。旋压技术属先进成形技术,通过对各项工艺参数的分析、研究,以及缺点的分析,可合理选择和优化工艺参数,提高产品质量提供有效方法和可靠依据。目前尚晞科技的铝合金车轮旋压技术水平已成熟,并实现了铝合金旋压轮毂的批量生产。 轮毂升级改装要怎么做?重庆铝合金改装车轮毂参考价
在中国改装车轮毂合法吗?杭州单片式改装车轮毂按需定制
轮毂不同制造工艺的区别:重力铸造非常简单,将液态的金属倒进轮毂模具中冷却成型。这种铸造方式效率非常高,成本也低,但是质量比较差,由于轮毂的各部分分布不是很均匀,而且金属内部分子的密度比较低,所以轮毂的强度不高,碰撞后很容易出现断裂的情况;低压铸造是在重力铸造的基础上进行了一个升级,将液态的金属倒入模具之后,给它施加一个恒定的压力,使金属的分子密度增高,轮毂成型之后会有更高的强度,且低压铸造的工艺也非常成熟,所以目前大部分车型上的轮毂采用的都是低压铸造工艺;旋压铸造是将铸造后的轮毂进行一个二次加工,将轮毂一边加热一边进行旋压加工,这样可使轮毂内的金属分子更加紧密,强度也更高。所以,这三种工艺的轮毂重量,旋压轮毂<低压铸造轮毂<重力铸造轮毂。 杭州单片式改装车轮毂按需定制
上海尚晞数控科技有限公司是一家有着先进的发展理念,先进的管理经验,在发展过程中不断完善自己,要求自己,不断创新,时刻准备着迎接更多挑战的活力公司,在上海市等地区的机械及行业设备中汇聚了大量的人脉以及**,在业界也收获了很多良好的评价,这些都源自于自身的努力和大家共同进步的结果,这些评价对我们而言是比较好的前进动力,也促使我们在以后的道路上保持奋发图强、一往无前的进取创新精神,努力把公司发展战略推向一个新高度,在全体员工共同努力之下,全力拼搏将共同上海尚晞数控科技供应和您一起携手走向更好的未来,创造更有价值的产品,我们将以更好的状态,更认真的态度,更饱满的精力去创造,去拼搏,去努力,让我们一起更好更快的成长!
上一篇: 北京重型数字油缸报价表
下一篇: 北京国内高精密数字油缸用在哪