液氮微量润滑技术厂商
由于微量润滑技术能够有效地降低切削区温度和减少刀具磨损,从而延长了刀具的使用寿命。研究表明,采用微量润滑技术的刀具寿命比传统切削液润滑的刀具寿命提高了20%以上。这对于降低生产成本、提高生产效率具有重要意义。在金属切削加工过程中,刀具与工件之间的摩擦和磨损会导致加工表面质量下降。微量润滑技术通过喷射微小油滴,能够更好地渗透到切削区,形成一层保护膜,减少刀具与工件之间的直接接触和磨损,从而提高加工表面质量。此外,微量润滑技术还能够减少切削过程中的烟雾和粉尘,改善工作环境。微量润滑技术可以有效地降低摩擦阻力、减少磨损,因此可以有效地延长设备的使用寿命。液氮微量润滑技术厂商
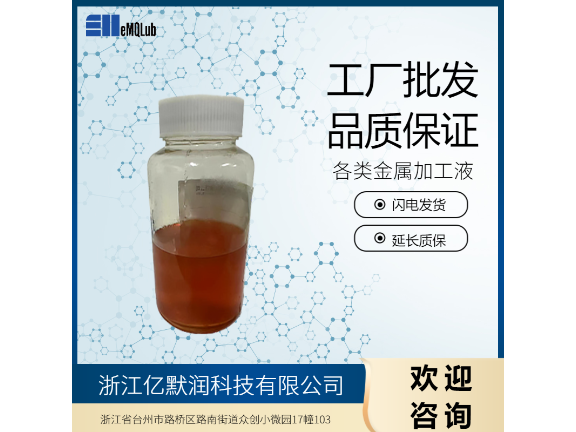
刀具微量润滑技术可以通过喷射、刷涂、浸渍等多种方式实现润滑剂的供给,便于实现自动化生产。通过将刀具微量润滑技术与数控系统、传感器等自动化设备相结合,可以实现刀具润滑的实时监控和自动调节,提高生产效率和加工精度。刀具微量润滑技术可以有效地降低刀具与工件之间的摩擦,减少刀具磨损。研究表明,采用刀具微量润滑技术后,刀具磨损可降低20%~50%。此外,刀具微量润滑技术还可以减少切削过程中产生的热量,降低刀具的热变形,进一步降低刀具磨损。刀具微量润滑技术可以有效地提高加工精度和加工效率,从而提高产品质量。通过采用刀具微量润滑技术,可以实现高速、高效、高精度的切削加工,保证产品的尺寸精度、表面质量和几何形状精度。此外,刀具微量润滑技术还可以减少切削过程中产生的热量和振动,避免加工过程中的缺陷和损伤,进一步提高产品质量。无锡锯切应用微量润滑技术企业齿轮微量润滑加工技术采用微量润滑系统,可以实现对齿轮加工过程的精确控制,从而提高生产效率。
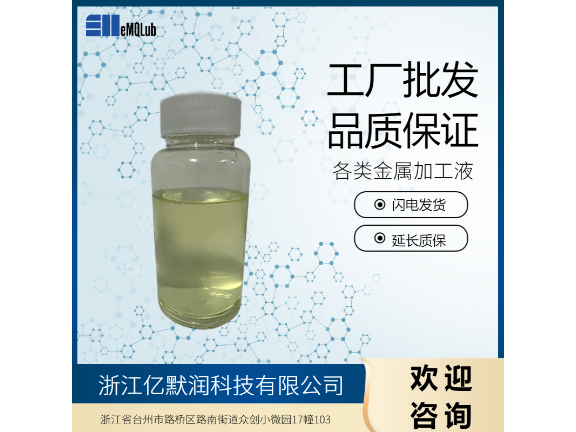
在传统的切削加工过程中,由于缺乏有效的润滑,刀具与工件之间的摩擦和磨损非常严重。这不只降低了刀具的使用寿命,而且影响了加工精度。微量润滑技术通过在刀具和工件之间施加一层薄薄的润滑膜,有效地减小了刀具与工件之间的摩擦,从而延长了刀具的使用寿命。研究表明,采用微量润滑技术的刀具寿命比传统切削加工方法提高了30%以上。在传统的切削加工过程中,由于刀具与工件之间的摩擦和磨损,加工精度容易受到影响。微量润滑技术通过减小刀具与工件之间的摩擦,有效地降低了加工过程中的误差,从而提高了加工精度。此外,微量润滑技术还可以减小切削力,使切削过程更加稳定,有利于提高加工精度。
刀具在切削过程中,由于摩擦和磨损,会导致刀具寿命的降低。传统的润滑方式往往无法满足高速切削的需求,而刀具微量润滑技术则可以有效地减少刀具与工件之间的摩擦,降低切削力,从而延长刀具的使用寿命。研究表明,采用刀具微量润滑技术后,刀具寿命可提高20%~50%。在高速切削过程中,由于刀具与工件之间的摩擦和磨损,容易导致加工精度的降低。刀具微量润滑技术可以有效地减少刀具与工件之间的摩擦,降低切削力,从而保证加工精度的稳定性。此外,刀具微量润滑技术还可以减少切削过程中产生的热量,降低刀具的热变形,进一步提高加工精度。微量润滑技术的较大优势就是节能环保。
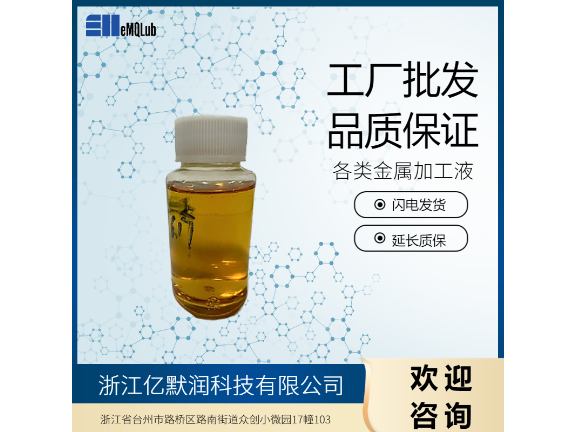
微量润滑加工技术具有很好的通用性,可以适应多种材料的加工。无论是金属材料、非金属材料还是复合材料,都可以采用微量润滑加工技术进行加工。这使得微量润滑加工技术在现代制造业中具有普遍的应用前景。传统的润滑冷却方法中,需要对切削液进行循环处理,工艺流程较为复杂。而微量润滑加工技术采用极少量的润滑剂进行加工,无需对切削液进行循环处理,工艺流程得到简化,降低了生产成本。由于微量润滑加工技术可以有效地降低切削热,减小刀具磨损,延长刀具寿命,因此,它可以有效地降低能耗。据统计,采用微量润滑加工技术后,能耗可以降低20%以上。微量润滑技术则通过精确控制润滑剂的使用量,使其在需要的地方形成薄薄的一层,从而实现高效润滑。液氮微量润滑技术厂商
车铣微量润滑技术可以有效地减少切削过程中的摩擦和磨损,从而降低工件表面的粗糙度,提高加工质量。液氮微量润滑技术厂商
高速主轴微量润滑技术可以有效地延长刀具寿命、提高加工效率和加工质量,从而降低生产成本。首先,采用微量润滑技术的刀具寿命比传统润滑方式的刀具寿命提高了30%以上,降低了刀具的更换频率和刀具成本。其次,采用微量润滑技术的加工效率比传统润滑方式的加工效率提高了15%以上,降低了加工时间成本。较后,采用微量润滑技术的加工质量比传统润滑方式的加工质量提高了20%以上,降低了废品率和返工率。综上所述,高速主轴微量润滑技术可以有效地降低生产成本。液氮微量润滑技术厂商
上一篇: 上海蜗轮微量润滑设备
下一篇: 常州碳素钢微量润滑设备