不沾涂层碳化钨喷涂表面处理
超音速火焰喷涂碳化钨喷涂在瓦楞辊上的应用一、热喷涂碳化钨在瓦楞辊上的应用A. 新型瓦楞辊喷涂碳化钨B、旧瓦楞辊改造为碳化钨瓦楞辊C、碳化钨瓦楞辊的修复 新型碳化钨瓦楞辊的涂层厚度为0.05-0.1mm。长期使用后涂层减少,无法生产时,我们会为您去除残留的碳化钨并进行修复。瓦楞辊的直径几乎没有变化。2、碳化钨瓦楞辊加工工艺碳化钨瓦楞辊的工艺与传统瓦楞辊不同。之前的基体热处理硬度不同,对喷涂前的齿形精度要求更高。它必须在全自动数控磨削上完成。其次,喷涂技术是保证碳化钨硬度的关键。后续抛光处理的结合力和质量,**难加工的是喷涂后的抛光技术。由于瓦楞辊不同于一般工件、齿形的独特性和碳化钨极高的表面硬度(如金刚石),传统的普通砂轮磨削根本无法进行。→研磨→(中频淬火)→喷砂→预热→打底→喷涂碳化钨(厚度0.05~0.06mm)→抛光研磨——寿命20-5000万跑米;常州卡奇的碳化钨喷涂是否结实耐用?不沾涂层碳化钨喷涂表面处理
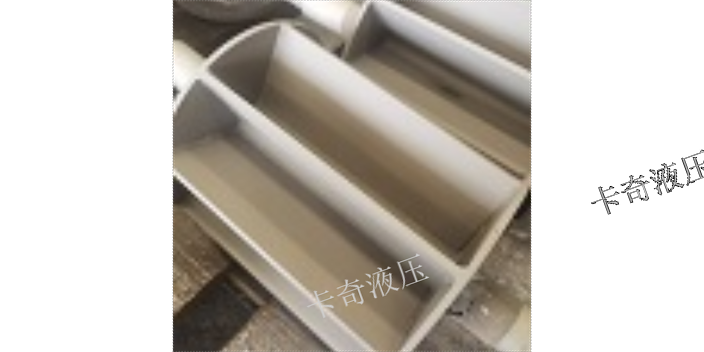
然而,热喷涂有两种工艺制程,分别为「等离子喷涂」与「电弧喷涂」,其应用也不太相同,以等离子喷涂而言,所喷涂的材料为氧化铝和氧化钇涂层,主要用来抵抗等离子的轰击造成腔体的损坏。另外一种电弧式喷涂的工艺则是喷涂纯铝线,使腔体内部表面具有高粗糙度,经过前列放电的效果来捕捉腔体内部的带电粒子,防止这些粒子影响良率。在航天产业中常见的涂层有抗高温的热障涂层、可磨耗涂层、耐高温金属涂层(T400、T800)、耐磨耗涂层等。其中,热障涂层主要由两个涂层组合而成,分别为「键结层,bondcoating」和「顶层,topcoating」,而这两种涂层所使用的热喷涂工艺也不相同。以键结层而言,目前常见的工艺有「低压等离子喷涂,lowpressureplasmaspraying,LPPS」、「高压高速火焰,highvelocityoxygenfuel,HVOF、HVAF」。 安徽高硬度碳化钨喷涂价格寻找碳化钨喷涂的专业生产厂家。
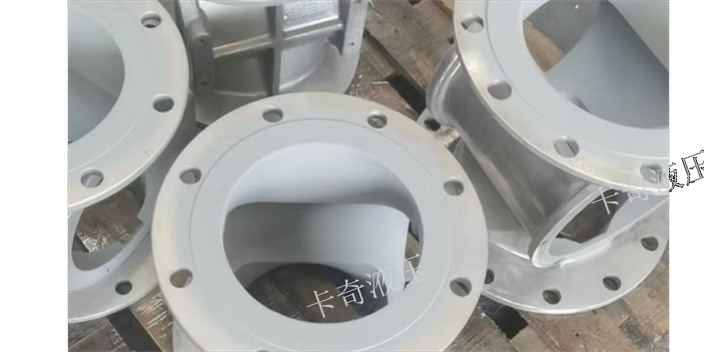
接下来介绍碳化钨喷涂特点:高硬度,耐磨,耐腐蚀主营业务:热喷涂,碳化钨喷涂,陶瓷喷涂,电弧喷涂,等离子喷涂,超音速火焰喷涂,冷喷涂;合金涂层,金属涂层,氧化物涂层,生物涂层;应用于航空航天、发电、汽车、石油石化、半导体、水处理、机械制造、医疗器具、再制造、替代镀铬等领域。表面处理技术除热喷涂外,还包括火焰喷焊、冷喷涂、激光熔敷、等离子堆焊、热处理、气相沉积、真空离子镀、微弧氧化、电镀、刷镀等工艺。
碳化钨喷涂的普及越来越广,应用的地方也是越来越多。对于碳化钨喷涂设备来说使用寿命、保证设备正常运行、降低企业能耗等方面的加强完善越来越重要。接下里和壹佰一起了解碳化钨喷涂要遵循那些工艺流程。碳化钨喷涂施工应遵循以下工艺流程:表面清洗:使用钢丝球机械手段进行操作,并且加上有碱性的洗涤液去清洗表面,可以主要采用钢丝球等机械手段,辅以碱性清洗液,去除管道表面锈蚀和油污等表面浮力层,清洁度达到SA3级,保证牢固的粘结基础。涂层。表面粗化:通常采用喷砂和电拉拔来提高涂层与基体之间的机械结合强度。标准粗糙度为6.5-25。喷底层:底层膨胀系数与基材非常接近,主要提高工作层的结合强度和抗热震性。常州卡奇的碳化钨喷涂质量可靠吗?
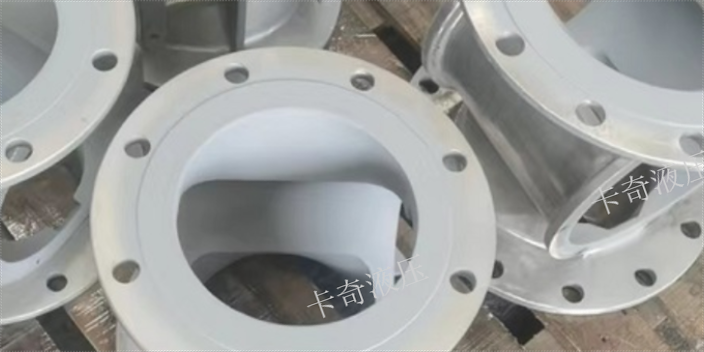
碳化钨有许多潜在的应用,包括热喷涂碳化钨涂层。这些碳化钨涂层在高性能汽车的制动盘上很常见。在应用中,碳化钨涂层改善了性能和维护间隔,减少了制动粉尘。碳化钨重要的应用之一是制造加工工具。这些工具利用了材料的耐磨性和耐热性。它们通常用于高精度或批量生产,如钢磨损过快。这种材料或其变体通常用于设计中的碳化钨钴复合材料,如刺穿装甲。碳化钨的强度在采矿和基础钻孔中也很常见。在运动中,它通常用作登山杖或滑雪杖的前列材料。喷涂碳化钨通常用于佩戴珠宝和手术设备。在后一种应用中,它提供了比不锈钢更好的性能,但更贵,需要更精细的处理。常州卡奇碳化钨喷涂服务质量。安徽高硬度碳化钨喷涂价格
碳化钨喷涂去哪找?常州卡奇告诉您。不沾涂层碳化钨喷涂表面处理
为了解决工艺辊的腐蚀磨损问题,不改变基材成分的表面处理是目前常用的工艺措施。例如,通过渗透镀、热喷焊、热喷涂技术等在工艺辊表面形成涂层。涉及的涂层材料包括W-Mo合金、铁-铝金属间化合物、WC-Co系列金属陶瓷、其中,以HVOF碳化钨为的喷涂材料已广泛应用于热镀锌汽车板生产线。工艺辊表面喷涂碳化钨后,可很大提高带钢表面质量。HVOF制备的碳化钨涂层具有良好的结合力,为基材提供了良好的保护。但是,如果喷涂失败并剥落,辊体的基材将直接暴露在外面,导致其迅速失效。因此,为了保证喷涂层能够更好地保护辊系,获得更好的带钢表面质量,有必要对喷涂层失效的原因及影响因素进行研究。不沾涂层碳化钨喷涂表面处理
上一篇: 陶瓷喷涂哪家好
下一篇: 上海耐磨碳化钨喷涂报价