金属锻件磁粉探伤检测
金属无损探伤测试是指利用各种物理原理和技术手段,对金属材料进行非破坏性检测和评估的方法。它可以在不破坏金属材料的情况下,检测出材料中的缺陷、裂纹、气孔、夹杂物等缺陷,并对其进行定性和定量分析,以评估金属材料的质量和安全性能。金属无损探伤测试的主要方法包括以下几种:1. 超声波探伤:利用超声波在材料中传播的特性,检测材料中的缺陷、裂纹、气孔等缺陷。2. 射线探伤:利用X射线或伽马射线穿透金属材料,检测材料中的缺陷、裂纹、气孔等缺陷。3. 磁粉探伤:利用磁场对金属材料进行磁化,通过观察磁粉在材料表面的分布情况,检测材料中的裂纹和缺陷。4. 涡流探伤:利用涡流感应原理,对金属材料进行检测,检测材料中的裂纹、气孔等缺陷。金属材料检测是确保金属制品质量和安全的重要环节,有助于提高产品的可靠性和持久性。金属锻件磁粉探伤检测
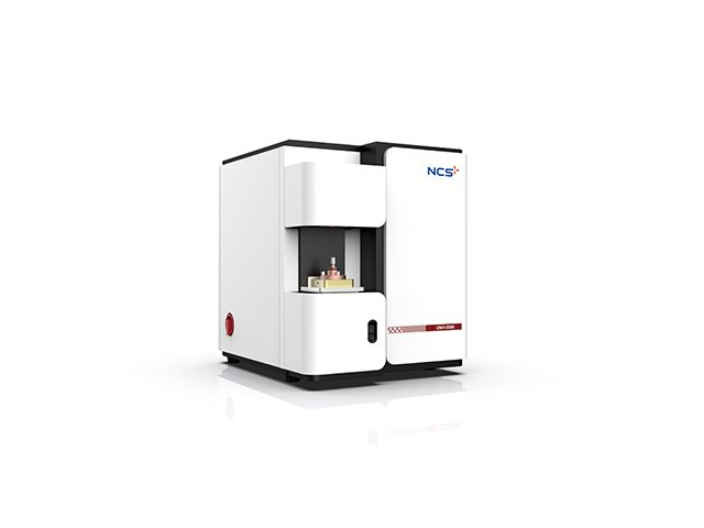
金属棒材表面检测的作用是什么?金属棒材表面检测是指对金属棒材表面进行检测,以确定其表面是否存在缺陷、裂纹、划痕、氧化等问题。金属棒材表面检测的作用是为了检查金属棒材表面是否存在缺陷,如裂纹、气孔、夹杂物、表面不平整等问题,以确保金属棒材的质量符合要求。这些缺陷可能会影响金属棒材的性能和寿命,甚至可能导致金属棒材在使用过程中出现断裂等安全问题。因此,对金属棒材进行表面检测是非常重要的。常用的金属棒材表面检测方法包括视觉检测、涂漆法、磁粉探伤、超声波探伤等。金属锻件磁粉探伤检测机械零部件机械性能测试是指通过一系列测试和试验,对机械零部件进行评估和验证的过程。
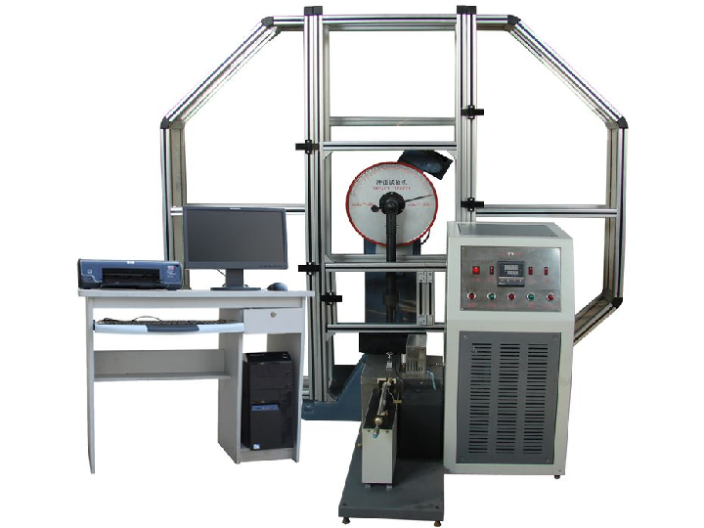
金属板材无损探伤测试需要注意什么?金属板材无损探伤测试需要注意以下几点:1. 选择适当的探伤器:不同的金属板材探测深度和探测灵敏度不同,需要选择适当的探伤器。2. 准备工作:金属板材表面应该清洁干净,确保表面没有任何杂质和油脂等,以免影响探伤结果。3. 控制环境:金属板材无损探伤测试需要在一定的温度和湿度条件下进行,以保证测试结果的准确性。4. 注意安全:在进行金属板材无损探伤测试时,需要注意安全,避免探伤器和测试人员受到伤害。5. 数据分析:金属板材无损探伤测试得到的数据需要进行分析,以确定金属板材的质量和可用性。需要注意的是,金属板材无损探伤测试需要专业的设备和技术,建议由专业的无损检测机构或工程师进行测试。
有色金属金相分析是什么呢?有色金属金相分析是一种通过显微镜观察金属材料组织和结构的方法,以了解其性能和质量。有色金属金相分析方法主要应用于铜、铝、镁、钛等有色金属材料的研究和生产过程中的质量控制。通过有色金属金相分析,可以观察到金属材料的晶粒大小、晶界、相含量、缺陷等信息,从而判断其材料性质是否符合要求。有色金属金相分析通常需要使用金相显微镜、切割机、研磨机、腐蚀液等设备,同时需要对样品进行切割、研磨、腐蚀等处理,以便于显微观察。金属材料检测能够发现金属材料中的缺陷、裂纹或其他不可见的内部问题。
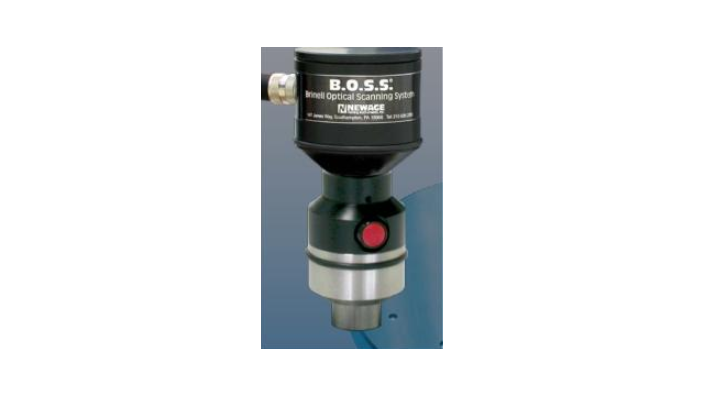
金属材料检测方法:磁粉检测是一种常用的金属材料检测方法,其原理是基于磁场的变化来检测金属材料内部的缺陷。在磁场作用下,金属材料内部的缺陷会对磁场产生影响,使磁场发生变化。通过在金属材料表面撒上磁粉,可以观察到磁粉在缺陷处的聚集情况,从而判断金属材料内部是否存在缺陷。超声波检测是一种利用超声波进行金属材料检测的方法,其原理是基于超声波在材料中传播的特性。超声波在金属材料中的传播速度和材料的密度、弹性模量等物理参数有关。当超声波遇到材料内部的缺陷、裂纹等问题时,会发生反射、折射、衍射等现象,通过对超声波的传播和反射信号进行分析,可以确定金属材料内部的缺陷位置和形态。通过金属材料检测,可以确保金属制品的符合规定的化学成分和力学性能。金属锻件磁粉探伤检测
磁粉检测可以有效地检测出金属表面和近表面的裂纹。金属锻件磁粉探伤检测
金属材料检测的发展趋势是什么?金属材料检测的发展趋势包括以下几个方面:1. 非破坏性检测技术的发展:随着科技的不断进步,非破坏性检测技术得到了普遍应用,如超声波检测、磁粉检测、涡流检测等,这些技术可以在不破坏材料的情况下检测出材料的缺陷和性能。2. 自动化检测技术的应用:自动化检测技术可以提高检测效率和准确性,减少人为因素的干扰,如机器视觉技术、智能化检测系统等。3. 多模态检测技术的发展:多模态检测技术可以结合多种检测手段,提高检测的准确性和可靠性,如结合超声波和磁粉检测等。4. 无损检测技术的应用:无损检测技术可以在不破坏材料的情况下检测出材料的缺陷和性能,减少了材料的浪费和成本,如红外热像技术、激光检测技术等。5. 数据分析技术的应用:数据分析技术可以对检测数据进行处理和分析,提高检测的准确性和可靠性,如人工智能技术、大数据分析技术等。金属锻件磁粉探伤检测
上一篇: 湖州金属锻件抗疲劳性能检测大概多少钱
下一篇: 河北金属线材无损探伤测试