渗碳热处理过程
正火热处理是一种常见的金属材料加工方法,其基本原理是将金属材料加热至临界温度后进行冷却,以获得理想的组织和性能。正火热处理的作用主要有以下几个方面:1.改善金属材料的机械性能。正火热处理可以使金属材料的硬度、强度和韧性等机械性能得到改善,从而提高其使用寿命和耐久性。2.改善金属材料的物理性能。正火热处理可以改善金属材料的导热性、导电性和磁性等物理性能,从而提高其使用效率和性能稳定性。3.改善金属材料的化学性能。正火热处理可以改善金属材料的耐腐蚀性和化学稳定性,从而提高其使用寿命和使用安全性。4.改善金属材料的加工性能。正火热处理可以改善金属材料的可加工性和可焊性,从而提高其加工效率和加工质量。高温回火组织的回火索氏体,它是由粒状渗碳体和等轴形铁素体组成混合物。渗碳热处理过程
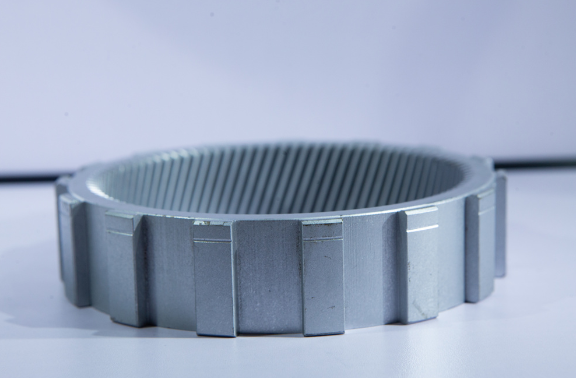
回火是对淬火后的材料进行加热处理,以降低硬度,提高韧性和可加工性。淬火是一种快速冷却的过程,使材料的晶粒细化,硬度增加,但韧性和可加工性降低。回火的目的是通过加热使材料的晶粒长大,减少内部应力,提高韧性和可加工性,同时降低硬度,使材料更加适合特定的应用。回火的原理是通过加热使材料的晶粒长大,减少内部应力,提高韧性和可加工性。回火温度和时间的选择取决于材料的成分和应用要求。通常,回火温度在200-700℃之间,时间在数小时到数十小时之间。回火的过程中,材料的硬度随着温度的升高而降低,但韧性和可加工性随着温度的升高而增加。回火的作用是使材料更加适合特定的应用。例如,高硬度的钢材适用于制造刀具和轴承等强度高要求的零件,但其韧性和可加工性较差,不适合制造需要弯曲和变形的零件。通过回火处理,可以降低钢材的硬度,提高其韧性和可加工性,使其更加适合制造需要弯曲和变形的零件。回火热处理哪家好对于某些高淬透性的钢,空冷即可淬火,如采用回火软化既能降低硬度,又能缩短软化周期。
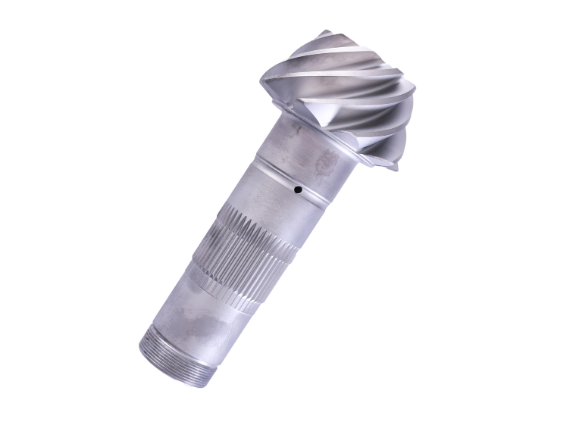
热处理具备处理小零件的能力。小零件往往具有较高的精度要求和复杂的形状结构,需要通过热处理来实现其性能的优化和稳定。首先,热处理可以改善小零件的硬度和耐磨性。小零件往往用于高速运动的机械设备中,需要具备较高的硬度和耐磨性。而通过热处理,可以使小零件的晶粒细化,晶界清晰,从而提高其硬度和耐磨性,使其更加耐用。其次,热处理可以改善小零件的韧性和抗拉强度。小零件往往需要承受较大的拉伸力和冲击力,需要具备较高的韧性和抗拉强度。而通过热处理,可以使小零件的组织结构得到优化,从而提高其韧性和抗拉强度,使其更加稳定和可靠。
预清洗可以减少热处理过程中的气体和液体反应,从而减少热处理过程中的气泡和裂纹。预清洗可以提高热处理的一致性,使得不同批次的材料热处理效果更加一致。因此,预清洗是确保热处理质量的重要步骤之一。在进行预清洗时,需要注意一些技术要求和注意事项。首先,需要选择合适的清洗方式和清洗剂。不同的材料和工艺要求需要选择不同的清洗方式和清洗剂。其次,需要控制清洗时间和温度。清洗时间和温度过长或过高会对材料产生不良影响。需要对清洗后的材料进行干燥处理。干燥处理可以去除材料表面的水分,防止水分对热处理产生不良影响。淬火按淬火部位:整体淬火、局部淬火、表面淬火等。
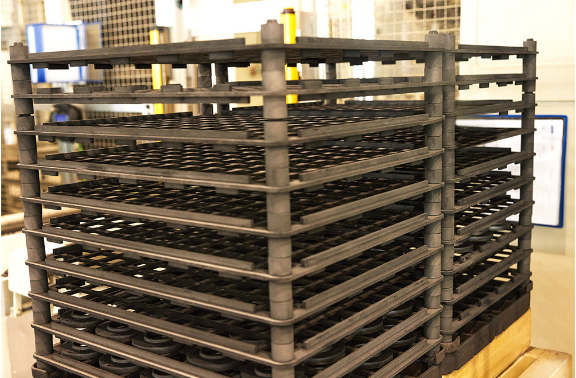
通过钢热处理,可以使钢材的性能得到明显提升,从而提高产品的质量和使用寿命。此外,钢热处理还可以改善钢材的加工性能,使其更易于加工和成型,从而降低生产成本。随着科技的不断进步和工业的不断发展,钢热处理技术也在不断创新和改进。目前,钢热处理技术已经发展到了智能化、自动化的阶段,可以通过计算机控制和监测系统来实现精确的加热和冷却过程,从而提高处理效率和产品质量。此外,钢热处理技术还在不断拓展应用领域,如在新能源、环保等领域中的应用也越来越普遍。可以预见,随着技术的不断进步和应用的不断拓展,钢热处理技术将会在未来的发展中发挥越来越重要的作用。一般用于锻件、铸件和焊接件。退火一般安排在毛坯制造之后,粗加工之前进行。江苏回火热处理条件
表面淬火后零件表面将产生很大的残余压应力,因而使材料的疲劳强度较大程度上提高。渗碳热处理过程
感应加热是一种高效、节能的加热方式,普遍应用于金属热处理领域。在热处理过程中,感应加热可以快速、均匀地加热金属,使其达到所需温度,然后通过冷却来改变其结构和性能。感应加热的优点在于其加热速度快、能量利用率高、加热温度可控、加热区域可调等特点,使其成为热处理领域中不可或缺的一种技术。感应加热在热处理中的应用包括淬火、回火、退火、正火等多种工艺。其中,淬火是常见的一种热处理工艺,其目的是通过快速冷却来使金属达到高硬度和强度高。感应加热可以快速加热金属到淬火温度,然后通过水、油等冷却介质来实现淬火。此外,感应加热还可以用于回火、退火等工艺,通过控制加热温度和时间来改变金属的组织结构和性能。渗碳热处理过程