电气机械制造业物料追溯系统操作方法
金属制品业物料追溯系统是一种利用先进的信息技术手段,对金属制品从原材料采购、入库、加工、组装到成品出库等全生命周期进行记录和追踪的管理系统。该系统通过赋予每一批物料独一的身份标识(如二维码或RFID标签),实时采集并存储各个环节的数据信息。在金属制品生产中,其重要作用表现在:一是实现物料来源与去向的透明化管理,确保原料质量合规、过程可控;二是快速定位问题物料,有效应对质量问题或产品召回事件,降低企业风险;三是通过对物料流转数据的深度分析,优化库存管理,减少浪费,提高整体运营效率。数字化物料管理系统应用覆盖了集成的需求计划、采购、存货仓储等有关物料管理所有任务。电气机械制造业物料追溯系统操作方法
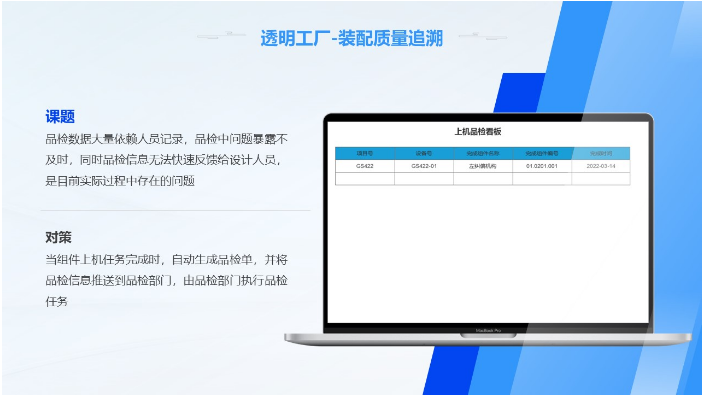
数字化品检管理系统是一种基于现代信息技术的先进质量管理工具,旨在提升产品检测的准确度与效率。该系统通过集成自动化检测设备、机器视觉技术、物联网数据采集以及AI算法分析等手段,实时监控生产线上每一道工序的产品质量参数,并对不合格品进行快速识别和隔离。它将传统的手动品检流程转化为智能化、标准化的过程,实现了从原材料进厂到成品出厂的全链条质量控制。此外,数字化品检管理系统还能生成详尽的质量报告,为企业的持续改进和决策提供有力的数据支持,从而有效降低废品率,提高产品质量稳定性,增强市场竞争力。上海仪器仪表制造业物料管理系统价格MES系统能够优化物料管理和库存控制,减少库存积压和浪费。
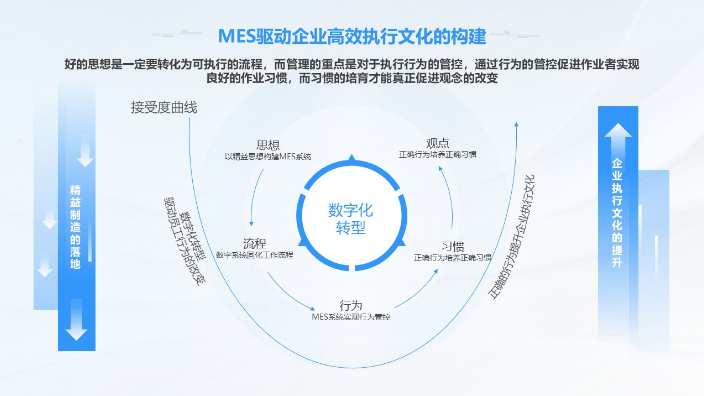
数字化生产管理系统如何赋能企业的生产管理和业务发展?数字化生产管理系统通过对生产各个环节进行深度数字化改造,极大地提升了企业的生产管理水平和市场响应能力。首先,它实现了生产数据的实时获取与分析,使得管理者能够准确掌握生产进度、物料消耗、设备状态等信息,便于做出快速有效的决策。其次,系统支持灵活排产和定制化生产,满足了市场的多元化需求。再者,通过对供应链的集成管理,提高了协同效率,降低了库存成本。此外,通过对生产设备的预测性维护,延长使用寿命,减少停机时间。
数字化品检管理系统是一种集成了先进信息技术和品质管理理念的综合性工具。该系统通过自动化、智能化的手段,对生产过程中的产品品质进行全方面、高效的监控和管理。它利用数字化技术,实现了从原材料入库到产品出厂的全程品质追溯,确保每一环节都符合品质标准。在数字化品检管理系统中,质检数据被实时采集、存储和分析,形成了一套完整的品质数据库。这使得品质管理人员能够迅速掌握生产过程中的品质状况,及时发现并处理潜在问题。同时,系统还提供了强大的数据分析功能,通过对历史数据的挖掘和比对,帮助企业发现品质问题的根源,制定针对性的改进措施。数字装备的普及应用将导致管理体制、生产方式、产品结构和产业结构的改变。
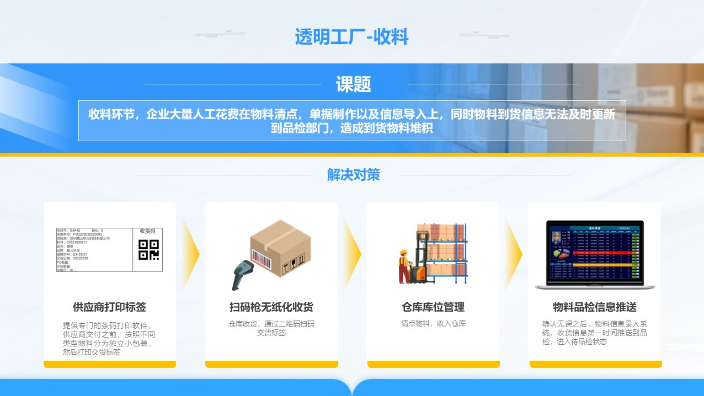
数字化生产管理系统是一种利用现代信息技术对生产过程进行全方面、实时管理和优化的解决方案。该系统集成了数据采集、分析预测、决策支持和执行监控等功能,将企业从设计、采购、生产、质量控制到物流等各个环节的数据进行统一管理,形成了一套高效、透明、智能化的操作体系。1. 数据采集与处理:通过连接生产线上的各种设备和传感器,实时获取生产实绩、物料消耗、设备状态等大量数据,并利用大数据技术进行快速准确地处理。2. 生产计划与排程:根据销售预测、库存状况以及生产资源约束条件,自动制定科学合理的生产计划,并动态调整生产排程以应对市场变化。3. 质量管控:实现产品全生命周期的质量追溯,通过对关键质量指标的实时监测,确保产品质量稳定并能迅速响应质量问题。4. 设备维护与预警:运用物联网技术和人工智能算法预测设备故障,提前安排预防性维护,降低设备停机时间,保障生产的连续性和稳定性。5. 供应链协同:通过集成ERP、MES等系统,加强与供应商、客户的信息共享与协同合作,提升供应链的整体效率。智能生产线MES管理系统能够提供供应链管理功能,帮助企业优化供应链的运作和协调。金属制品业物料管理系统多少钱
智能生产线物料管理系统能够减少人工操作和错误,降低生产成本。电气机械制造业物料追溯系统操作方法
数字化生产管理系统是现代制造业转型升级的重要推手。该系统通过构建统一的数据平台,实现了生产数据的实时采集、传输和处理,打破了传统生产模式中信息孤岛的限制。它运用大数据、云计算等先进技术,对生产过程中的各种数据进行深入挖掘和分析,为企业提供了全方面的生产监控和决策支持。数字化生产管理系统还能够根据市场需求和生产条件的变化,灵活调整生产计划和资源配置,确保企业在激烈的市场竞争中保持重要地位。此外,该系统还具备高度的可扩展性和可定制性,能够满足不同行业和企业的个性化需求,推动制造业向更高水平的数字化、智能化发展。电气机械制造业物料追溯系统操作方法
上一篇: 上海仪器仪表制造业品检管理系统使用规范
下一篇: 上海数字化生产管理系统操作方法