数控机床主轴维修定期回访
在罗茨风机的维修过程中,对风机的基座和减震装置的检查也不能忽视。基座要能够承受风机的重量和运行时产生的振动,检查基座是否有裂缝、下沉或者变形的情况。减震装置要起到有效的减震作用,查看减震弹簧的弹性是否正常,减震垫是否老化、损坏。如果基座或减震装置出现问题,会导致风机运行时的振动增大,影响设备的稳定性和使用寿命。及时修复或更换有问题的基座和减震装置,能保证风机的平稳运行。罗茨风机机械设备的定期保养对于预防故障、延长使用寿命具有重要意义。制定科学合理的保养计划,按照规定的时间间隔对风机进行清洁、紧固、润滑等保养工作。定期清理风机内部的灰尘和杂物,防止其进入关键部件影响运行。对连接件进行紧固,防止松动导致振动和噪声。按时更换润滑油和易损件,如油封、密封垫等。通过有规律的保养,可以及时发现潜在问题,降低故障发生的概率。定期检查电主轴的机械结构,确保其安全性。数控机床主轴维修定期回访
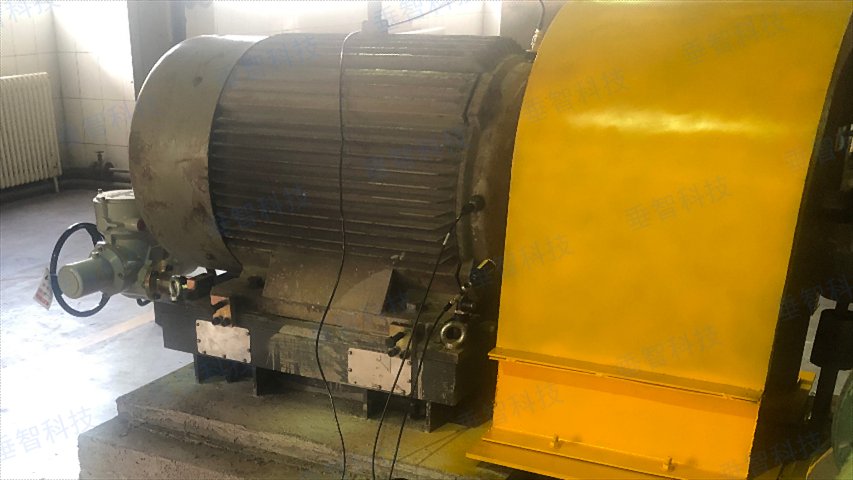
罗茨风机的维修还需关注其齿轮和轴承。齿轮的啮合情况直接影响到传动的精度和稳定性。检查齿轮的齿面是否有磨损、点蚀或者胶合的痕迹,若存在这些问题,会导致传动噪音增大、效率降低。同时,要确保齿轮的轴向和径向间隙符合要求,过大或过小都会影响齿轮的正常运转。对于轴承,需要检查其润滑状况,润滑油不足或变质会使轴承磨损加剧。此外,观察轴承是否有过热、异响或者振动异常的现象,这些都可能是轴承损坏的征兆。及时更换磨损或损坏的齿轮和轴承,能有效避免故障的进一步扩大。数控机床主轴维修定期回访电主轴的维修需要使用专业的工具和设备。
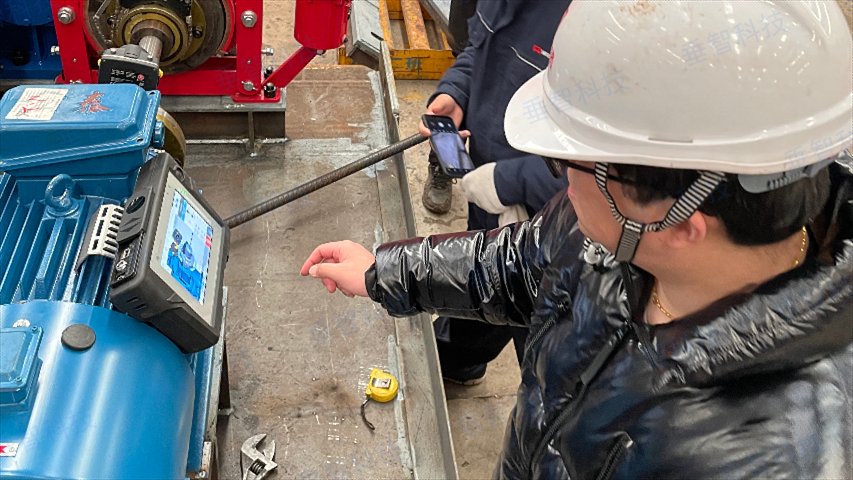
永磁电机的轴承维修不容忽视。首先,通过手感或者听诊器判断轴承运转时是否有异常的噪音和振动。如果有,可能意味着轴承磨损或者损坏。拆卸轴承时,要小心操作,避免对其造成二次伤害。检查轴承的滚珠或滚柱,看表面是否有剥落、划痕或者锈蚀。同时,测量轴承的游隙,过大或过小的游隙都会影响电机的运行精度和稳定性。在永磁电机机械设备的维修过程中,电机的绝缘性能检测是重要的一步。使用兆欧表测量电机的绝缘电阻,确保其数值在规定范围内。绝缘性能下降可能会导致漏电、短路等严重故障。对于长期运行的电机,要特别留意绝缘材料的老化情况,及时更换老化的绝缘部件,保障电机的安全运行。
永磁电机的磁路检查也是维修工作的一部分。检查永磁体的安装是否牢固,有无位移或者脱落的现象。同时,查看磁路中是否有异物或者铁屑,这些杂质可能会干扰磁场分布,影响电机的性能。清理磁路上的杂物,保持磁路的畅通和纯净。永磁电机的磁路检查也是维修工作的一部分。检查永磁体的安装是否牢固,有无位移或者脱落的现象。同时,查看磁路中是否有异物或者铁屑,这些杂质可能会干扰磁场分布,影响电机的性能。清理磁路上的杂物,保持磁路的畅通和纯净。一次风机的维修工作,需要耐心和细心,缺一不可。
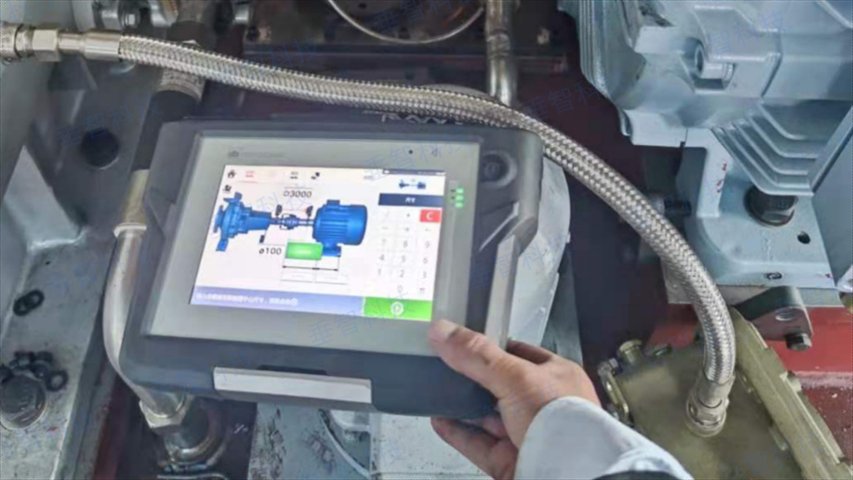
维修锅炉风机机械设备时,对于风机的传动部件也要格外关注。检查皮带的张紧度是否合适,过松会导致皮带打滑,影响传动效率;过紧则会增加皮带和轴承的磨损。如果使用的是联轴器,要检查联轴器的同轴度和连接螺栓的紧固情况。同轴度偏差过大可能会引起振动和噪声,连接螺栓松动则可能导致传动失效。对这些传动部件的精心维护,能保证风机的动力传递稳定可靠。在锅炉风机机械设备的维修过程中,叶轮的平衡调整是一个重要的步骤。叶轮在长期运行后,可能会因为磨损、积灰或者制造缺陷等原因失去平衡。通过专门的平衡检测设备,可以发现叶轮的不平衡量。然后,采取相应的措施,如在叶轮较轻的部位添加配重,或者对磨损严重的部位进行修复、更换,以使叶轮恢复平衡。叶轮的平衡对于减少风机的振动、降低噪音和延长使用寿命都有着至关重要的作用。一次风机维修中,发现叶轮磨损严重,需及时更换。锅炉风机设备维修经济效益
一次风机出现异响,维修人员迅速查找原因。数控机床主轴维修定期回访
维修真空泵机械设备时,对其阀门和管道的检查也十分重要。阀门的开关是否灵活,密封性能是否良好,都直接影响到真空泵的工作效率和真空度的保持。管道是否有泄漏、堵塞或者弯曲变形的情况,都会影响气体的流动和压力的传递。特别是在一些关键的连接部位,要仔细检查密封垫和密封圈的状态,确保没有气体泄漏。对于发现的问题,要及时更换损坏的阀门和管道部件,保证系统的密封性和流畅性。真空泵机械设备维修完成后,进行严格的测试和调试是必不可少的环节。首先,进行空载测试,观察泵的运转是否平稳,声音是否正常,温度是否在合理范围内。然后,逐渐增加负载,检测真空度是否能够达到设计要求。在测试过程中,要密切关注各项参数的变化,如电流、电压、压力等。对于出现的异常情况,要及时分析原因并进行调整。只有经过充分的测试和调试,确保设备性能稳定可靠,才能将其投入正常使用。数控机床主轴维修定期回访