山东高浓度电镀废水技术
投资与运行费用分析表明:工程运行1年多即可收回RO浓缩镍的设备费用。液膜法并不是采用传统的固相膜,而是悬浮于液体中很薄的一层乳液颗粒,是一种类似溶剂萃取的新型分离技术,包括制膜、分离、净化及破乳过程。美籍华人黎念之博士发明了乳状液膜分离技术,该技术同时具有萃取和渗透的优点,把萃取和反萃取两个步骤结合在一起。乳化液膜法还具有传质效率高、选择性好、二次污染小、节约能源和基建投资少的特点,对电镀废水中重金属的处理及回收利用有着良好的效果。吸附法是利用比表面积大的多孔性材料来吸附电镀废水中的重金属和有机污染物,从而达到污水处理的效果。镀层性能不同于基体金属,具有新的特征。根据镀层的功能分为防护性镀层,装饰性镀层及其它功能性镀层。山东高浓度电镀废水技术

4)容积负荷高。由于硝化阶段采用了强化生化,反硝化阶段又采用了高浓度污泥的膜技术,有效地提高了硝化及反硝化的污泥浓度,与国外同类工艺相比,具有较高的容积负荷。(5)缺氧/好氧工艺的耐负荷冲击能力强。当进水水质波动较大或污染物浓度较高时,本工艺均能维持正常运行,故操作管理也很简单。通过以上流程的比较,不难看出,生物脱氮工艺本身就是脱氮的同时,也降解酚、氰、COD等有机物。结合水量、水质特点,我们推荐采用缺氧/好氧(A/O)的生物脱氮(内循环)工艺流程,使污水处理装置不但能达到脱氮的要求,而且其它指标也达到排放标准。江西高浓度电镀废水清洗水冷却系统发生不正常现象时,立即采取措施,确保鼓风机不发生故障;
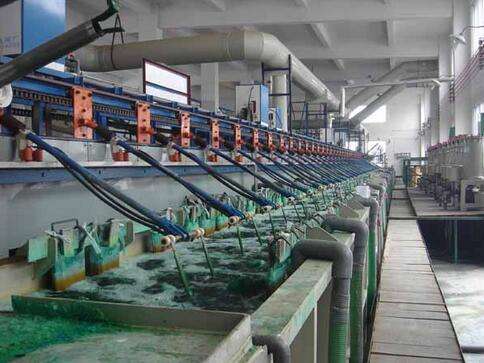
节约水资源以及保护环境是我们保护家园的很大作用。所以电镀废水处理至关重要.本文综述了各种电镀废水处理技术的优缺点膜分离技术主要包括微滤(MF)、超滤(UF)、纳滤(NF)、反渗透(RO)、电渗析(ED)、液膜(Lv)等,利用膜的选择透过性来对污染物进行分离去除。该方法去除效果好,可实现重金属回收利用和出水回用,占地面积小,无二次污染,是一种很有发展前景的技术,但是膜的造价高,易受污染。
对膜技术在电镀废水处理中的应用和效果进行了分析,结果表明:结合常规废水处理工艺与膜生物反应器(MBR)组合工艺,电镀废水被处理后的水质达到排放标准;电镀综合废水经UF净化、RO和NF两段脱盐膜的集成工艺处理后,水质达到回用水标准,RO和NF产水的电导率分别低于100gS/cm和1000gS/cm,COD分别约为5mg/L和10mg/L;镀镍漂洗废水通过RO膜后,镍的浓缩高达25倍以上,实现了镍的回收,RO产水水质达到回用标准。
化学方法是通过化学反应来处理废水。常用的化学方法有中和、沉淀、氧化和还原等。中和是指通过加入碱性或酸性物质来调节废水的酸碱度,使其达到中性。沉淀则是通过加入沉淀剂使废水中的污染物形成沉淀,从而达到净化废水的目的。氧化和还原是通过加入氧化剂或还原剂将废水中的有机物进行氧化或还原反应,将其转化为较为稳定的物质。生物方法是利用微生物对废水中的污染物进行降解和去除。常用的生物方法有好氧法和厌氧法。好氧法是指将废水中的有机物通过微生物的呼吸作用进行降解和去除。重金属是许多工业活动和化学反应产生的危险污染物之一。它们可以对环境和人类健康造成极大的危害。

电镀污泥处理多少钱一吨电镀污泥是电镀行业中产生的一种废弃物,通常含有大量有害物质,例如重金属、有机物等,对环境带来极大的污染风险。为了减少电镀污染的影响,需要进行处理。处理电镀污泥的成本因不同情况而异,主要分为两类,一类是固体废物处理,另一类是危险废物处理。对于固体废物处理,通常包括机械处理、渗透过滤、高温烧毁等多个环节,在处理的过程中产生的场地租赁、劳动力、运输费等成本,一般在2000元至3000元/吨之间。对于危险废物处理,其涉及到更为严格的处置标准和流程要求,一般采用高温、高压的技术进行处理,处理成本通常在3000元至5000元/吨之间,其处理难度和成本均高于固体废物。使镀液中欲镀金属的阳离子在基体金属表面沉积出来,形成镀层的一种表面加工方法。广西含铬电镀废水处理设备安装
2.可以应用于各种水源:重金属去除剂也可以用于净化地下水。山东高浓度电镀废水技术
电镀废水处理工艺很多:20世纪70年代流行树脂交换,80年代电解法、化学法+气浮等。根据我厂20年来在电镀废水处理实践中得出,树脂交换对处理贵稀金属离子废水、回收贵稀金属有它的优越性。电解法:能耗高,电耗和铁耗均高,对高浓度含铬废水产生污泥量太多,不适应,同时对含氰废水处理不理想,所以含氰废水还要用化学法。化学药剂+气浮法:采用化学药品氧化还原中和,用气浮上浮方法进行泥水分离,因电镀污泥比重大,并且废水中含有多种有机添加剂,实际使用时气浮分离不彻底,并且运行管理不便,到90年代末,气浮法应用越来越少。山东高浓度电镀废水技术
上一篇: 广西全自动电镀废水清洗
下一篇: 内蒙古全自动电镀废水监测方案