品牌膜厚仪推荐
在初始相位为零的情况下,当被测光与参考光之间的光程差为零时,光强度将达到最大值。为探测两个光束之间的零光程差位置,需要精密Z轴向运动台带动干涉镜头作垂直扫描运动或移动载物台,垂直扫描过程中,用探测器记录下干涉光强,可得白光干涉信号强度与Z向扫描位置(两光束光程差)之间的变化曲线。干涉图像序列中某波长处的白光信号强度随光程差变化示意图,曲线中光强极大值位置即为零光程差位置,通过零过程差位置的精密定位,即可实现样品表面相对位移的精密测量;通过确定最大值对应的Z向位置可获得被测样品表面的三维高度。这种膜厚仪可以测量大气压下 。品牌膜厚仪推荐
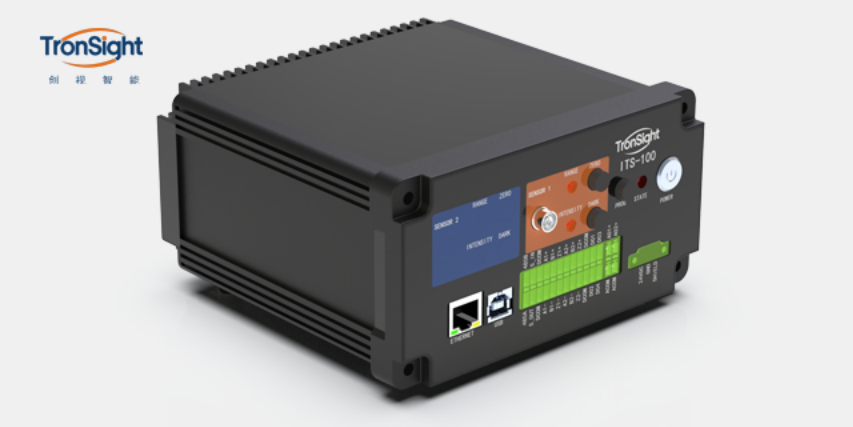
通过基于表面等离子体共振传感的测量方案,结合共振曲线的三个特征参数,即共振角、半高宽和反射率小值,反演计算可以精确地得到待测金属薄膜的厚度和介电常数。该方案操作简单,利用Kretschmann型结构的表面等离子体共振实验系统即可得到共振曲线,从而得到金膜的厚度。由于该方案为一种强度测量方案,受环境影响较大,测量结果存在多值性问题,因此研究人员进一步对偏振外差干涉的改进方案进行了理论分析,从P光和S光之间相位差的变化来实现厚度测量。品牌膜厚仪推荐厂家随着技术的进步和应用领域的拓展,白光干涉膜厚仪的性能和功能将不断提高和扩展 。
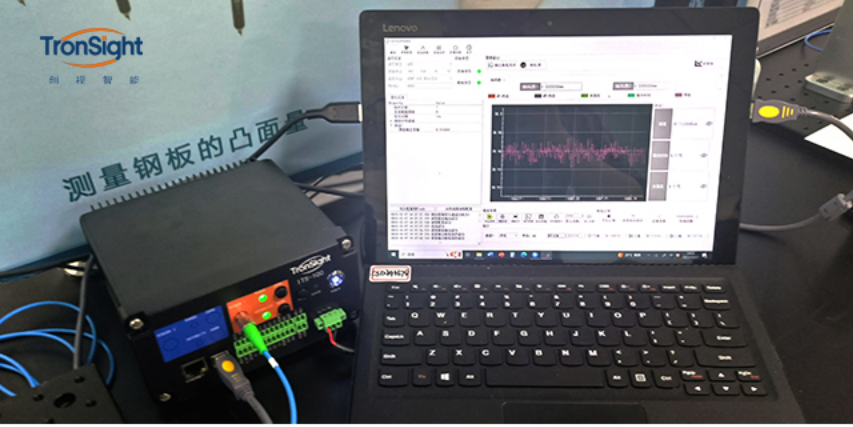
在激光惯性约束核聚变实验中,靶丸的物性参数和几何参数对靶丸制备工艺改进和仿真模拟核聚变实验过程至关重要。然而,如何对靶丸多个参数进行同步、高精度、无损的综合检测是激光惯性约束核聚变实验中的关键问题。虽然已有多种薄膜厚度及折射率的测量方法,但仍然无法满足激光核聚变技术对靶丸参数测量的高要求。此外,靶丸的参数测量存在以下问题:不能对靶丸进行破坏性切割测量,否则被破坏的靶丸无法用于后续工艺处理或打靶实验;需要同时测得靶丸的多个参数,因为不同参数的单独测量无法提供靶丸制备和核聚变反应过程中发生的结构变化的现象和规律,并且效率低下、没有统一的测量标准。由于靶丸属于自支撑球形薄膜结构,曲面应力大、难以展平,因此靶丸与基底不能完全贴合,可在微观区域内视作类薄膜结构。
莫侯伊膜厚仪在半导体行业中具有重要的应用价值膜厚仪的测量原理主要基于光学干涉原理。当光波穿过薄膜时,会发生干涉现象,根据干涉条纹的变化可以推导出薄膜的厚度。利用这一原理,通过测量干涉条纹的间距或相位差来计算薄膜的厚度。膜厚仪通常包括光源、光路系统、检测器和数据处理系统等部件,能够实现对薄膜厚度的高精度测量。在半导体行业中,薄膜的具体测量方法主要包括椭偏仪法、X射线衍射法和原子力显微镜法等。椭偏仪法是一种常用的薄膜测量方法,它利用薄膜对椭偏光的旋转角度来计算薄膜的厚度。X射线衍射法则是通过测量衍射光的角度和强度来确定薄膜的厚度和结晶结构。原子力显微镜法则是通过探针与薄膜表面的相互作用来获取表面形貌和厚度信息。这些方法各有特点,可以根据具体的测量要求选择合适的方法进行薄膜厚度测量。薄膜的厚度对于半导体器件的性能和稳定性具有重要影响,因此膜厚仪的测量原理和具体测量方法在半导体行业中具有重要意义。随着半导体工艺的不断发展,对薄膜厚度的要求也越来越高,膜厚仪的研究和应用将继续成为半导体行业中的热点领域。白光干涉膜厚测量技术可以实现对薄膜的非接触式测量;
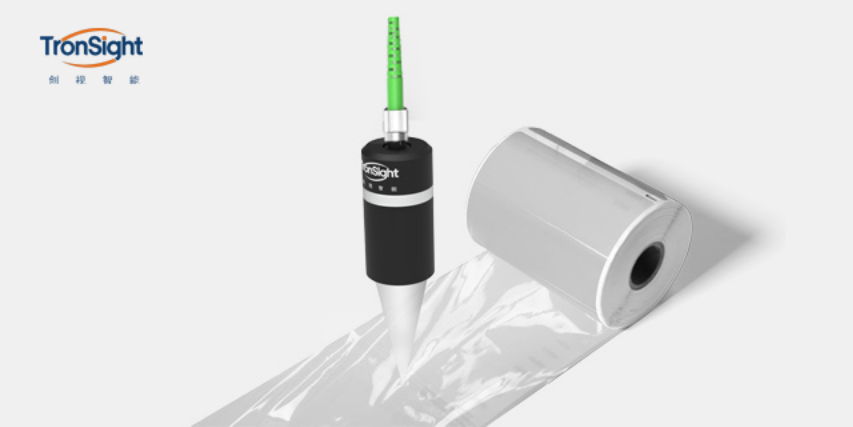
利用包络线法计算薄膜的光学常数和厚度,但还存在很多不足,包络线法需要产生干涉波动,要求在测量波段内存在多个干涉极值点,且干涉极值点足够多,精度才高。理想的包络线是根据联合透射曲线的切点建立的,在没有正确方法建立包络线时,通常使用抛物线插值法建立,这样造成的误差较大。包络法对测量对象要求高,如果薄膜较薄或厚度不足情况下,会造成干涉条纹减少,干涉波峰个数较少,要利用干涉极值点建立包络线就越困难,且利用抛物线插值法拟合也很困难,从而降低该方法的准确度。其次,薄膜吸收的强弱也会影响该方法的准确度,对于吸收较强的薄膜,随干涉条纹减少,极大值与极小值包络线逐渐汇聚成一条曲线,该方法就不再适用。因此,包络法适用于膜层较厚且弱吸收的样品。白光干涉膜厚仪需要进行校准,并选择合适的标准样品。测薄膜厚度 膜厚仪
可以配合不同的软件进行分析和数据处理,例如建立数据库、统计数据等;品牌膜厚仪推荐
在初始相位为零的情况下 ,当被测光与参考光之间的光程差为零时,光强度将达到最大值。为探测两个光束之间的零光程差位置,需要精密Z向运动台带动干涉镜头作垂直扫描运动或移动载物台,垂直扫描过程中,用探测器记录下干涉光强,可得白光干涉信号强度与Z向扫描位置(两光束光程差)之间的变化曲线。干涉图像序列中某波长处的白光信号强度随光程差变化示意图,曲线中光强极大值位置即为零光程差位置,通过零过程差位置的精密定位,即可实现样品表面相对位移的精密测量;通过确定最大值对应的Z向位置可获得被测样品表面的三维高度。品牌膜厚仪推荐
上一篇: 有哪些光谱共焦详情
下一篇: 防水膜厚仪安装操作注意事项