铝合金红冲加工有限公司
红冲工艺中的后期处理与质量控制也很关键,主要包括以下几个方面:质量检测:在转子红冲工艺完成后需对转子进行质量检测以确保其符合相关标准和要求。质量检测包括尺寸测量、形状检查、表面质量检查等方面。对于不符合要求的转子需进行返修或报废处理。质量控制:为确保转子红冲工艺的稳定性和产品质量的一致性需加强质量控制工作。通过制定严格的生产工艺规程和操作规程、加强设备维护和保养、提高员工技能水平等措施来降低产品质量风险提高生产效率和经济效益。红冲加工过程中,严格控制加热温度和时间,确保制件质量稳定。铝合金红冲加工有限公司
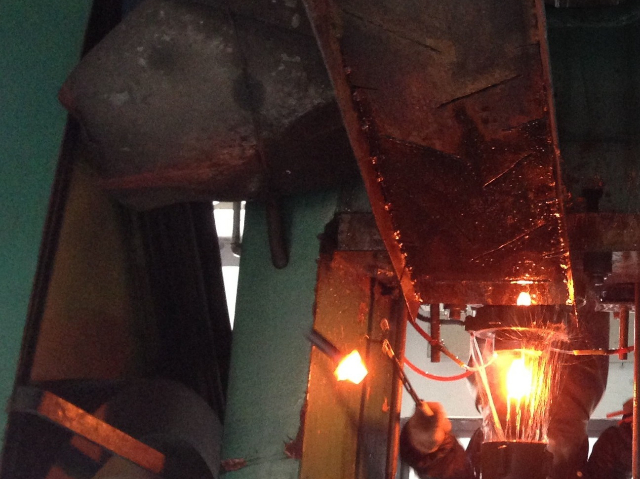
直齿轮红冲工艺缺点:模具成本高:红冲工艺对模具的要求较高,模具的设计和制造需要投入大量的资金和时间。同时,模具的维护和更换也是一笔不小的费用。工艺复杂:红冲工艺涉及多个环节,包括材料准备、加热、冲压成形、冷却和后续处理等。这些环节需要严格控制工艺参数,以确保齿轮的精度和质量。因此,红冲工艺的工艺过程相对复杂,需要经验丰富的技术人员进行操作。设备要求高:红冲工艺需要使用高精度、高压力的压力机和模具,这些设备的购置和维护成本较高。同时,设备的运行和维护也需要专业的技术人员进行。受原材料限制:红冲工艺对原材料的性能和质量有一定的要求。如果原材料的性能不稳定或质量不达标,将直接影响齿轮的成形质量和性能。环保问题:红冲工艺在加热和冲压过程中可能会产生噪音、振动和废气等环境问题。这些问题需要得到妥善解决,以确保生产过程的环保性和可持续性。铝合金红冲加工有限公司红冲工艺以其独特的优势,在金属成形加工领域展现出强大的竞争力。
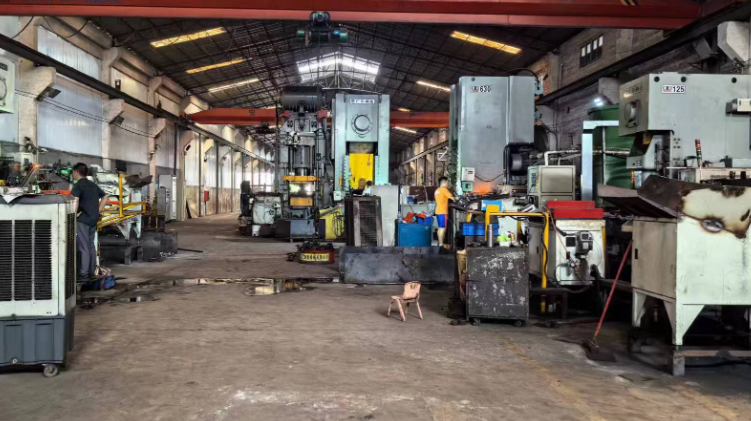
关于涨紧轮红冲(金属加工工艺)的市场需求量,由于这是一个相对专业的细分领域,直接的市场数据可能较为有限。行业背景与趋势金属加工行业增长:近年来,随着工业制造业的不断发展,金属加工行业整体呈现增长态势。特别是随着汽车、机械、航空航天等领域的快速发展,对精密金属零部件的需求不断增加,这也为涨紧轮红冲等金属加工工艺提供了广阔的市场空间。技术进步与国产化:随着金属加工技术的不断进步和国产化程度的提高,国内企业在这一领域的竞争力逐渐增强。红冲工艺作为一种先进的热压力加工工艺,其生产效率高、产品质量好,越来越受到市场的青睐。
尽管红冲工艺具有诸多优点,但在实际生产中仍面临一系列技术挑战。首先,加热过程中金属材料的氧化和脱碳问题一直是亟待解决的难题,这不仅影响产品的表面质量,还可能降低其力学性能。为解决这一问题,现代红冲工艺普遍采用保护气氛加热炉,如真空炉、惰性气体保护炉等,有效减少了材料在高温下的氧化和脱碳。其次,模具的设计与制造也是红冲工艺的关键环节,模具的精度、材料选择及热处理工艺直接决定了产品的形状精度和表面质量。因此,采用先进的CAD/CAM技术进行模具设计,以及选用强度高、高耐磨性的模具材料,并进行精密的热处理,成为提升红冲产品质量的重要手段。此外,针对大型复杂件的红冲成型,还需解决模具的开合、脱模以及冲压过程中的温度控制等难题,这要求工艺人员具备丰富的经验和创新精神。相比锻模,红冲的金属变形率更高,纤维组织状态更优。
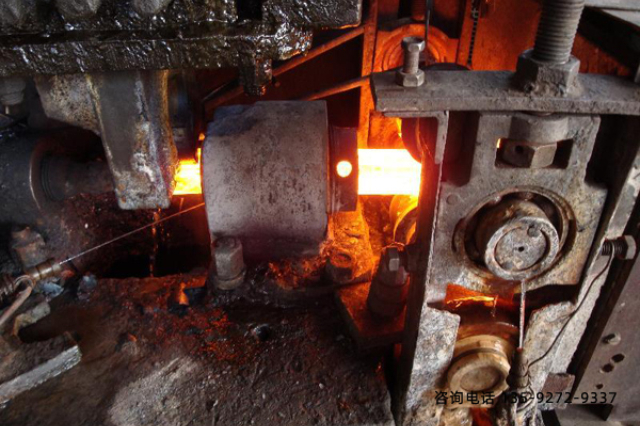
展望未来,红冲工艺将继续在金属加工领域发挥重要作用,并随着科技进步和市场需求的变化而不断进化。一方面,随着智能制造、物联网等技术的融合应用,红冲生产线将实现更高程度的自动化、智能化,提升生产效率与产品质量。另一方面,随着全球对可持续发展的重视,红冲工艺将更加注重节能减排、资源循环利用,推动行业向绿色化、低碳化方向发展。同时,红冲工艺作为人类智慧与技艺的结晶,其背后蕴含的工匠精神、创新精神和文化传承价值也不容忽视。在快速变化的现代社会中,我们应积极保护和传承这份宝贵的文化遗产,通过教育、展览、文化交流等多种形式,让更多人了解红冲工艺的魅力,激发年轻一代对金属加工技艺的兴趣与热爱,为这一古老工艺注入新的活力与希望。在未来的日子里,红冲工艺不仅将继续服务于现代工业的发展,更将成为连接过去与未来、传承与创新的重要桥梁。红冲工艺能有效提高机械零部件的机械强度和耐用性。精密红冲毛坯供应商
红冲工艺能够一次性压制出形状复杂的零部件,类似注射模成形。铝合金红冲加工有限公司
红冲操作:加热处理:在红冲操作中,首先将金属材料进行加热处理。加热温度需根据材料的种类和性能进行确定,一般控制在材料的临界温度以上。加热过程中需保持温度均匀、稳定,避免出现过热或过烧现象。加热完成后,需对金属材料进行保温处理,以确保其达到适宜的红冲温度。模具安装与调试:将加热好的金属材料放入模具中,并进行模具的安装与调试。在安装过程中需确保模具与设备的匹配性和密封性良好。在调试过程中需根据实际需要调整模具的位置和角度等参数,以确保金属材料能够顺利进入模具并成形。红冲成形:在模具安装和调试完成后进行红冲成形操作。通过压力机对模具施加一定的压力使金属材料在模具内发生塑性变形并逐渐充满模具型腔。在成形过程中需保持压力稳定、均匀分布并控制好成形速度和时间等参数以确保成形精度和产品质量。脱模与后处理:当金属材料完全充满模具型腔后需进行脱模操作。在脱模过程中需采用合适的脱模方式和工具以避免损坏转子和模具。脱模完成后还需对转子进行后处理如清理、去毛刺等以确保其表面质量和尺寸精度符合标准要求。铝合金红冲加工有限公司
上一篇: 20Cr锻件锻造制造有限公司
下一篇: 万向节锻件锻造制造单位