福州船用铸件
就工业铸造工艺来说,铜的熔点低,铸造简单。热铜液的流动性好,铸件气泡少,光洁度高,因此船用铸件螺旋桨材料几乎由铜合金垄断,用的较多的是镍铝青铜。目前船用螺旋桨采用不锈钢铸造也是有的,但是不锈钢件整体铸造技术难度过大。不锈钢的熔点高,所以铸造模具的耐火性也得提升。工业上有个经验公式,铸造温度每提高100度,成本加一倍。青铜熔点只有800度,而不锈钢熔点高达1700度,温度差了900度,铸造成本翻9倍。而且精密焊接和硬表面抛光的费用都加进去,这成本就贵得多了。所以不锈钢螺旋桨没有大规模普及。船用铸件的设计到产品需要预留的加工余量以及浇注的位置、型面的选择还有参数等等。福州船用铸件
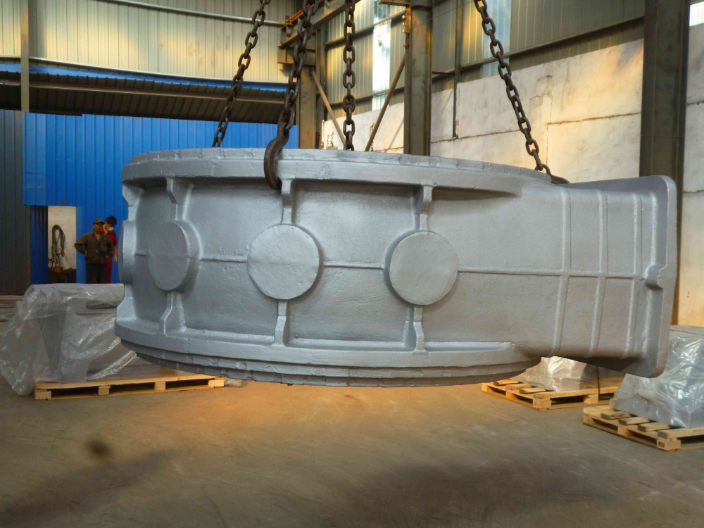
一些溶剂性涂料可以溶解船用铸件表面薄的油脂沉积物,使其与涂料混合且并无任何不利影响。但对于重油脂沉积或含水性涂料、无溶剂涂料却不适用。溶剂清洁一般用抹布,一旦弄脏可以频繁更换。后一道清洗一般都用新溶剂,如石脑油。有机溶剂严禁接触眼睛或皮肤,严禁附近有火星或明火,严禁非必要的吸入。溶剂清洁后的金属,一般需要在涂装之前再次清洁。喷砂通常是钢材或金属表面处理的较好方法。喷砂清洁法于其他清洁方法相比会明显增加涂装的使用年限。南京船用铸铁件供货费用船用铸件都是用来搭配机械设备使用的,所以产品的质量问题方面也必须要得到保障。
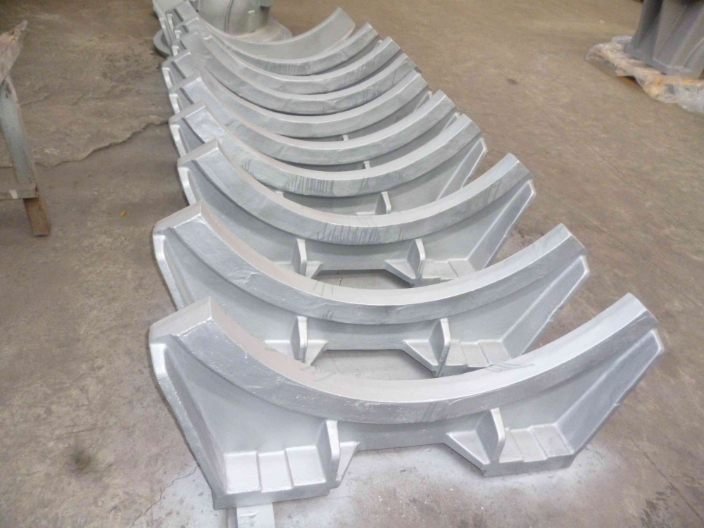
影响船用铸件磨损的因素有哪些呢?如何解决船用铸件磨损情况呢?船用铸件的硬度是影响其磨损的重要因素。一般而言,希望耐磨件的硬度高于磨料硬度的0.8倍以上,以获得较好的耐磨性。须特别说明,此耐磨件硬度是耐磨件工作面在磨损后的硬度,而非磨损前的初始硬度。但是耐磨件的硬度并非越高越好,某些工况下,过高的硬度易致显微裂纹的萌生。对显微切削机制的磨料磨损而言,提高船用铸件的硬度有利于耐磨性的提高。对疲劳剥落机制的磨料磨损而言,船用铸件较高的硬度与良好的延性和韧度配合,特别是与好的断裂韧度,低的裂纹扩展速率以及高的冲击疲劳抗力相配合,有利于耐磨性的提高。
对刚造的船用铸件的金属表面处理可选用抛丸或有机化学酸洗钝化解决。很多造船厂选用滚动式法防锈处理,将船用铸件用细铁丝扎成3m之上长的速状,放进滚桶内,筒内放进不锈钢丝锻、金刚砂,铜片碎渣等,用电机推动滚桶旋转,船用铸件遭受耐磨材料碰撞而去除锈迹。去除筒内和船用铸件上的锈迹烟尘,只能上漆。通常可吊入滴漆筒内开展喷涂工艺工程施工,3~5分钟后,吊着干躁。短喷涂间距二十四h,通常喷涂工艺3道。溶剂清洁法是去除表面油脂主要的方法。船用铸件表面的细微裂纹可用着色法、磁粉法检查。
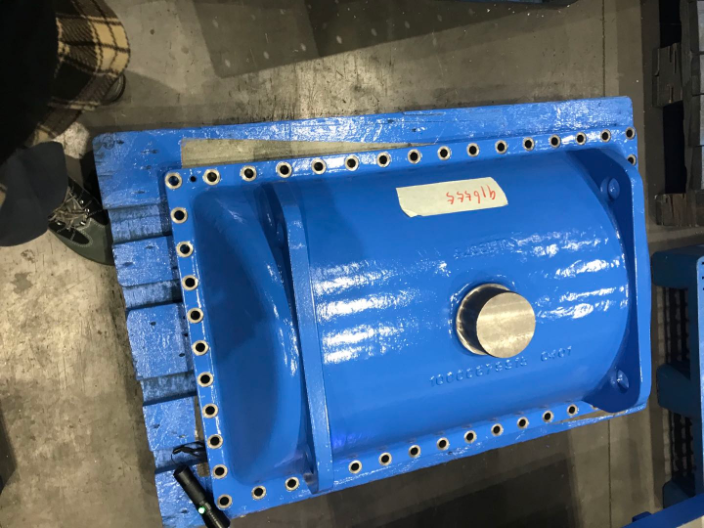
如何将船用铸件的缺陷损失降到较低:船用铸件在生产过程中,由于多种因素影响,常常会出现气孔、夹渣、裂纹、凹坑等缺陷。这时候为了使船用铸件能够达到使用标准,减少损失浪费,往往会对缺陷进行修复。常用的修补设备为氩弧焊机、电阻焊机、冷焊机等。对于质量与外观要求不高的船用铸件缺陷可以用氩弧焊机等发热量大、速度快的焊机来修补。但在精密船用铸件缺陷修补领域,由于氩焊热影响大,修补时会造成船用铸件变形、硬度降低、砂眼、局部退火、开裂、磨损、划伤、咬边、或者是结合力不够及内应力损伤等二次缺陷。冷焊机正好克服了以上缺点,其优点主要表现在热影响区域小,船用铸件无需预热,常温冷焊修补,因而无变形、咬边和残余应力,不会产生局部退火,不改变船用铸件的金属组织状态。船用铸件修补注意事项:凡拟采用焊补方法对船用铸件缺陷进行修补时,应审核缺陷情况和焊补工艺规程。杭州锚泊设备铸铁件供货报价
在加工的过程中,船用铸件的铸造工艺设计也是占据着非常重要的作用。福州船用铸件
在工业加工上,船用铸件螺旋桨就已经属于大型和超大型零件,螺旋桨表面曲面多,线条复杂,而要求的工艺指标为精度高于0.1mm,这就造成技术非常普通的民用螺旋桨,也难以用一般的车床、铣床加工成型;至于高精度螺旋桨,就更需要先进的高精度数控机床来加工。螺旋桨作为推进用的强力受力部件。其内部对强度的要求也高,不能有沙眼、气泡。因此大型螺旋桨的叶片,一般不能用锻压成型,目前工业上能使用的生产方式一般以高精度的铸造为主,一次浇铸成型然后用机械打磨抛光表面使其达到要求。福州船用铸件
江苏凯鑫铸造有限公司汇集了大量的优秀人才,集企业奇思,创经济奇迹,一群有梦想有朝气的团队不断在前进的道路上开创新天地,绘画新蓝图,在江苏省等地区的机械及行业设备中始终保持良好的信誉,信奉着“争取每一个客户不容易,失去每一个用户很简单”的理念,市场是企业的方向,质量是企业的生命,在公司有效方针的领导下,全体上下,团结一致,共同进退,**协力把各方面工作做得更好,努力开创工作的新局面,公司的新高度,未来江苏凯鑫铸造供应和您一起奔向更美好的未来,即使现在有一点小小的成绩,也不足以骄傲,过去的种种都已成为昨日我们只有总结经验,才能继续上路,让我们一起点燃新的希望,放飞新的梦想!
上一篇: 江苏精密机床床身铸件采购
下一篇: 双级往复式压缩机铸铁件供应费用