四川MES系统生产
国工智能MES系统是一套面向生产执行层的信息化管理系统,可以满足流程行业的生产管理需求,它能够帮助企业实现生产数据收集与分析、生产计划管理、生产过程监控、产品质量管理、生产工艺管理、BOM管理、看板管理和设备管理等功能,提高企业中制造车间的执行力。
过程追溯:MES系统会对每批产品都分配一个的批号,或者产品的ID,每当有质量问题发生时,可以通过产品ID或者批号追踪到该产品的生产记录,包含生产设备、生产人员、生产批次、生产开始时间、结束时间、生产时的工业参数等信息,还可以将这些信息统一汇总成报表,更方便生产管理者发现问题或者追溯同一批次产品。
质量管理:MES系统可以将生产过程中的质量检测的各信息统一与产品相关联,并能将质量检测信息汇总后在数据库中建立质量档案,管理者可以通过不同的检索条件对需要的内容进行检索,简单方便。 MES系统可以帮助企业实现生产过程的节能减排,降低能源消耗和环境污染。四川MES系统生产
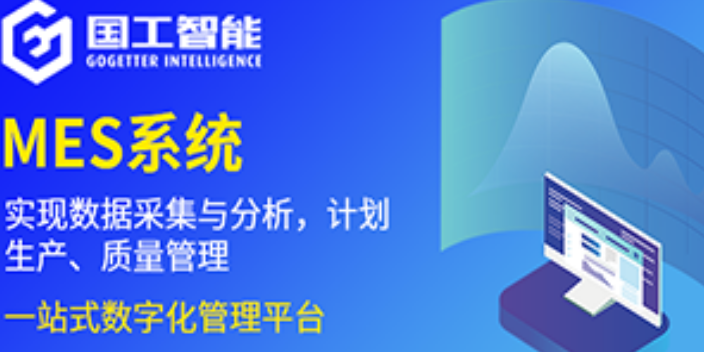
智能研发管理系统是先进的实验室检验及研发项目管理工具,但目前市面上的系统都只是处于信息记录层面,而国工实验室智能研发管理系统融合了国工智能数据大脑平台MAI,平台内提供上百种统计学相关算法及机器学习算法。通过这些算法对实验数据进行分类分析、聚类分析、关联分析、预测分析等方式,挖掘数据潜在价值,探索人力无法探知的规律,真正实现提高企业产品附加值及行业竞争力,助力企业快速发展。国工实验室管理系统LIMS和智能研发系统DPM,是国工智能制造管理平台(MES-MOM)的一部分。他们都以数据大脑平台为底层支撑,来提供算法支撑。四川MES系统生产MES系统可以帮助企业实现生产过程的智能化,提高企业的数字化能力和竞争力。

国工MES系统,是一套面向制造企业车间执行层的生产信息化管理系统。
生产过程追溯:
√提供长期的质量信息历史数据查询,及时发现生产过程中的质量问题。
√通过条码跟踪,实现关键物料的精确追溯。
MES通过反馈结果,来优化生产制造过程的管理业务,例如,当出现用户产品投诉的情况时,MES能够根据产品编码,追溯这批产品的所有生产过程信息,包括它的原料供应商,操作机台,操作人员,经过的工序,生产时间日期,和关键的工艺参数等,根据这些反馈信息及时做出调整,就能有针对性的为客户提供更好的服务。
首先是生产效率的提升:MES系统能够通过控制程序管理设备作业,同时实现生产数据的自动采集,从而解放人工劳动力,提高生产效率。它如同一个不知疲倦的助手,始终保持高效运转,帮助企业提升产能。
另外是产品质量的提升:MES系统能够稳定产品质量,通过减少手工统计和线下沟通,避免人为操作失误,从而提高产品质量。它如同一个严格的质检员,始终保持警惕,确保每一个产品都符合高质量标准。
促进企业信息化的转型:MES系统的模块化和异构系统兼容特性,非常适用于制造型企业、中小型企业,以及拥有较长自动化和信息化改造历史的传统行业(如:化工行业、医药行业、食品行业等)转型。它如同一个引导者,帮助企业在信息化转型的道路上稳步前行。 MES系统可以帮助企业实现生产过程的智能监管,提高生产过程的合规性和安全性。
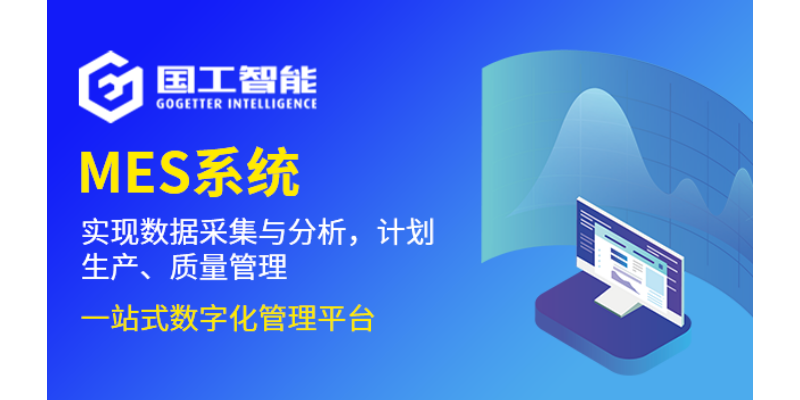
SOP(标准作业流程)
1、系统支持模板管理功能,可提供多种原始记录模板。2、支持系统管理员自定义添加原始记录模板,提供模板编辑器。用户可以在模板中定义文字、表格、图形、图片、勾选框、报告条码、页眉页脚、报告分页、logo、电子签名等,并能够按照需要配置原始记录内数据的修约规则。3、系统支持管理员可自定义修改、删除原始记录模板,修改记录及版本均在系统中留有记录,保证用户可以追溯到之前任意一个版本或原始记录,同时系统还记录每个版本的修改人,修改时间等。 MES系统可以帮助企业实现生产过程的可追溯性,方便质量管理和质量追溯。湖北MES软件功能
MES系统可以实现生产过程的智能调度,提高生产过程的调度效率和准确性。四川MES系统生产
MES (Manufacturing Execution System):生产制造执行系统,是整合制造资源、管理生产进度、质量、设备和人员绩效的制造业生产管理思想和管理工具。
应用需求:1.生产计划:MES系统通过对接ERP系统,将生产计划的相关信息获取到,可以制定与生产计划对应的生产工单,并通过对生产状况信息的获取,反馈给生产计划,让生产计划可以根据实际的生产情况做出相应的调整,使生产计划执行力度得到保障。2、工艺管理:MES系统根据不同的角色分配不同的权限,一些重要的信息只能有权限的人才可以看到,有效防止信息泄露,由于是生产工艺都录入在MES系统中,所以更改生产工艺只需更改系统中的文件即可,不需要手动更改纸档文件,方便快捷。 四川MES系统生产
上一篇: 陕西MES软件
下一篇: 北京实验室管理系统平台