河北软件MES系统
SOP(标准作业流程)
1、系统支持模板管理功能,可提供多种原始记录模板。2、支持系统管理员自定义添加原始记录模板,提供模板编辑器。用户可以在模板中定义文字、表格、图形、图片、勾选框、报告条码、页眉页脚、报告分页、logo、电子签名等,并能够按照需要配置原始记录内数据的修约规则。3、系统支持管理员可自定义修改、删除原始记录模板,修改记录及版本均在系统中留有记录,保证用户可以追溯到之前任意一个版本或原始记录,同时系统还记录每个版本的修改人,修改时间等。 MES系统可以实现生产过程的智能制造,提高生产过程的制造效率和产品质量。河北软件MES系统
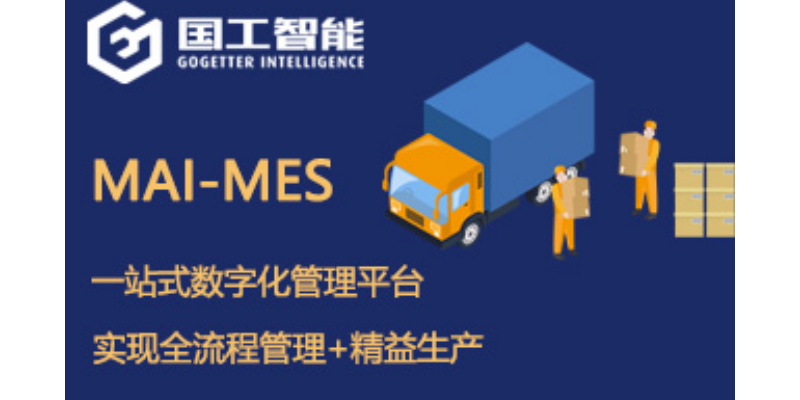
mes软件系统高效生产信息化管理系统:助力企业打造智能工厂,实现精益生产。
智能制造管理平台_mes软件_mes系统的功能:
4、实现数据可视化MES系统获取到的生产信息都可以通过报表展示出来,让生产状况及相关的信息在管理者面前一目了然。
5、拉动/推动生产以订单为源头,生产计划为依托,实现生产与销售的高效结合,促进生产效率提升,拉动/推动生产。
6、实现质量可追溯生产、物料、生产设备等信息数据都记录在一起,以条码为载体,做到质量可追溯化管理。 河南MES系统设计MES系统可以帮助企业实现生产过程的智能预测,提高生产计划的准确性和生产效率。
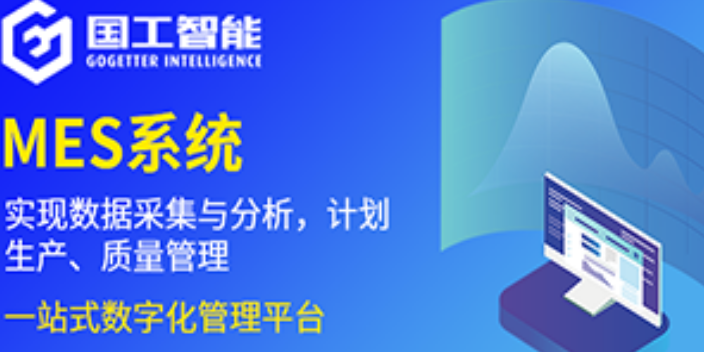
MES系统即制造企业生产过程执行系统,是一套面向制造企业车间执行层的生产信息化管理系统。MES 可以为企业提供包括制造数据管理、计划排产管理、生产调度管理、质量管理、工作中心、看板管理、生产过程控制、底层数据集成分析、生产大数据分析等管理模块,为企业打造一个扎实、可靠、可行的制造协同管理平台。
mes生产系统可以让企业资源信息的有效整合让企业各种资源信息有机整合在一起,时人力、物流、资金、设备等资源信息互相协作,达到资源的有效利用,提高价值。
mes系统的效益分析:
1、提升企业生产信息化能力将企业生产信息人工、物料、工艺、设备有机整合在一起,实现车间生产设备的集中控制管理,实现生产设备与计算机之间的信息交换,帮助企业实现设备及资源优化配置和重组,达到资源的利用,提高价值。
2、打通企业信息孤岛,提升生产透明化能力,通过数据采集接口获取并更新与生产过程相关的各种数据和参数,把生产相关的各种资源信息建立在一个统一的平台中,同时生成标准图表和报告直观反映当前或过去某段时间的加工状态。使管理者对车间生产状态、设备状态及加工信息一目了然,及时将管控指令下发车间,车间可以实时反馈执行状态,提高车间生产的透明化能力。
3、实现企业无纸化办公MES除了实现监测,还具备业务管理等功能,可以将车间控制层DCS,SCADA和管理经营层的ERP连接到一起,将车间生产过程中的生产相关的信息和过程集成起来统一管理,克服传统的手动录入及非必要的手动操作,实现生产数据文档电子化,打造无纸化管理。同时避免或减少基于纸质文档的人工传递及流转,保障工艺文档的准确性和安全性,为生产企业解决信息滞后,数据失真等问题。 MES系统可以帮助企业实现生产过程的智能控制,提高生产过程的控制效率和稳定性。
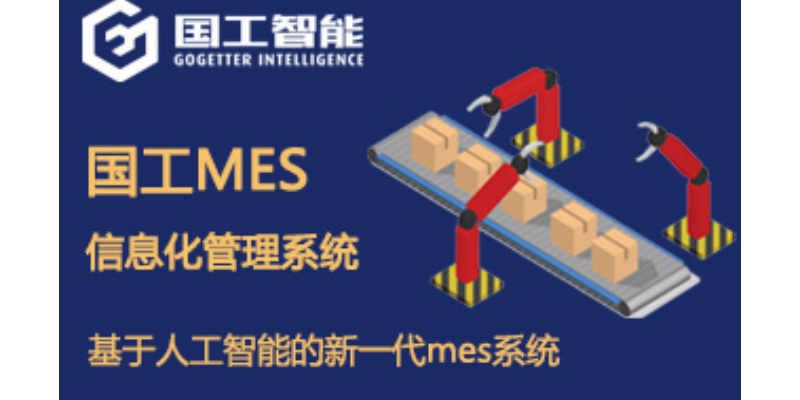
MES系统价值:1、企业资源有效整合:让生产资源信息有机整合在一起:人员、物料、设备等资源信息互相协作,达到资源的利用,提高生产效率。2、拉动/推动生产:以订单为源头,生产计划为依托,实现生产与销售的高效结合,促进生产效率提升,拉动/推动生产。3、实现质量可追溯:生产、物料、生产设备等信息数据都记录在一起,以条码为载体,做到质量可追溯化管理。4、打通信息孤岛:建立统—的生产加工数据存储中心,把生产相关的信息都存储在这个平台中,实时数据全局共享。5、实现多系统连接:MES系统可以与多种系统做对接,实现与软件系统的无缝结合,达到软件自动提取数据,自动处理数据功能。6、实现数据可视化:MES系统获取到的生产信息都可以通过报表展示出来,让生产状况及相关信息在管理者面前一目了然。国工智能制造管理系统是整合制造资源、管理生产进度、质量、设备和人员绩效的制造业生产管理思想、工具。河北软件MES系统
MES系统可以实现生产过程的智能控制,提高生产效率和产品质量。河北软件MES系统
九目项目组顺利完成了九目化学MES系统二期的交付,这是继九目化学MES系统一期、九目化学LIMS、九目化学DEV(智能研发管理系统)后,我们与九目化学股份有限公司的再一次合作。近日,在九目项目验收会上,我们还收获了来自甲方的认可——获得“九目化学供应商”的荣誉称号。在项目验收会上,国工智能总经理亲自出席会议发表重要讲话,并感谢客户对我们国工智能的信任与认可。双方领导就未来工业数字化智能化趋势等进行了深入的讨论。河北软件MES系统
上一篇: 四川MES软件开发
下一篇: 四川lims实验室管理系统价格