专注橡胶产品医用橡胶管
挤出(Crowdingout),一般根据所加工聚合物的类型和制品或半成品的形状,选定挤出机、机头和口模,以及定型和牵引等相应的辅助装置,然后确定挤出工艺条件如螺杆转速、机头压力、物料温度,以及定型温度、牵引速度等。在挤出过程中,物料一般都是要经过塑炼的过程,但定型方法也是有所不同。例如,挤出的塑料常需冷却定型,使其固化,从而挤出橡胶的半成品,则尚需进一步硫化。使用挤出工艺的产品有:橡胶密封条,胶管,橡套电缆。等等等等车窗密封条分有前后档风玻璃密封条、车窗玻璃导槽密封条和车窗内外侧条。专注橡胶产品医用橡胶管
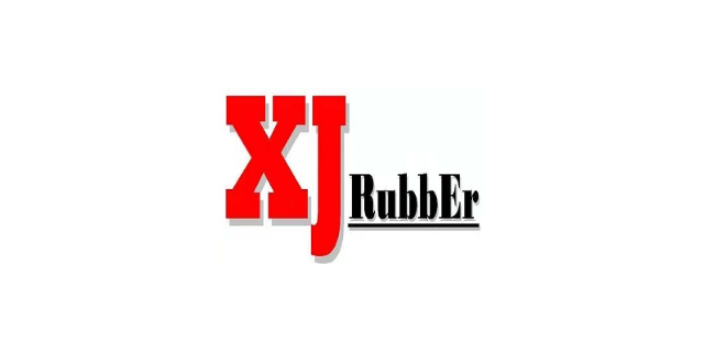
二、密封制品类1发动机曲轴后:以氟橡胶制(密封件)曲轴前:以丙烯酸橡胶制(密封件)膜片类:以丁腈橡胶或共聚氯醚橡胶,及三氟丙基甲基乙烯基硅橡胶制阀杆密封:以氟橡胶制(密封件)气缸盖衬垫:以丙烯酸橡胶制2.车身用挡风雨条:以三元乙丙橡胶制玻璃密封条:以三元乙丙橡胶制油口盖密封件:以丁腈橡胶制3.底盘用变速箱油封(密封件):以丙烯酸橡胶制动力转向油封(密封件):以丁腈橡胶制球形接头防尘罩:以聚氨酯橡胶或氯丁橡胶制CVJ用保护罩:以TPEE热塑弹性体制齿条齿轮保护罩:以TPO或TPEE热塑弹性体制制动MC用帽:以三元乙丙橡胶制卡式活塞密封(密封件):以三元乙丙橡胶制工业橡胶产品丁腈橡胶制品橡塑材料越轻,绝热效果越好;
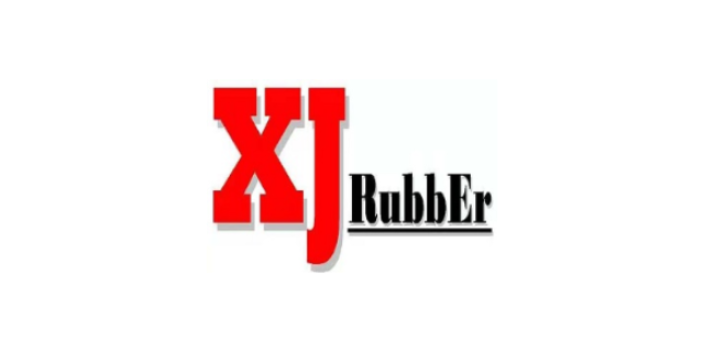
四、混炼为了适应各种不同的使用条件、获得各种不同的性能,也为了提高橡胶制品的性能和降低成本必须在生胶中加入不同的配合剂。混炼就是将塑炼后的生胶与配合剂混合、放在炼胶机中通过机械拌合作用使配合剂完全、均匀地分散在生胶中的一种过程。混炼是橡胶制品生产过程中的一道重要工序,如果混合不均匀就不能充分发挥橡胶和配合剂的作用影响产品的使用性能。混炼后得到的胶料人们称为混炼胶它是制造各种橡胶制品的半成品材料,俗称胶料通常均作为商品出售购买者可利用胶料直接加工成型、硫化制成所需要的橡胶制品。根据配方的不同?混炼胶有一系列性能各异的不同牌号和品种?提供选择。
国外的橡胶密封条均已采用三元乙丙橡胶制造,使用寿命也在15万公里以上。而国产密 封条的三元乙丙橡胶化尚未完全普及,一些用氯丁-天然橡胶制成的密封条使用寿命为3-5万公里。 国外已开发出智能化的橡胶制品。中国密封条企业应及时关注世界高分子智能材料和智能化橡胶制品的发展趋势,开发具有知识产权的智能化橡胶密封条,增强企业的竞争能力。 汽车密封用橡胶材料 目前汽车制造业中橡胶密封制品TPV挤出发泡采用的材料主要以氟橡胶、硅橡胶、丙烯酸酯橡胶、丁橡胶、三元乙丙橡胶、氯醇橡胶和氢化丁橡胶为主。在制造密封条的原材料中,以往采用的主要原材料三元乙丙橡胶也在不断更新和发展。
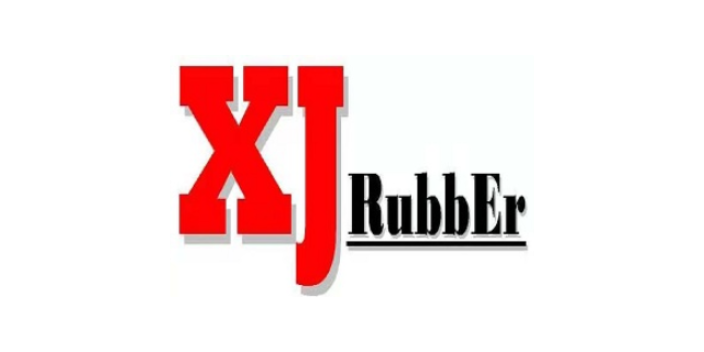
三、塑炼生胶富有弹性,缺乏加工时必需的可塑性性能,因此不便于加工。为了提高其可塑性,所以要对生胶进行塑炼,这样在混炼时配合剂就容易均匀分散在生胶中,同时在压延、成型过程中也有助于提高胶料的渗透性渗入纤维织品内和成型流动性。将生胶的长链分子降解形成可塑性的过程叫做塑炼。生胶塑炼的方法有机械塑炼和热塑炼两种。机械塑炼是在不太高的温度下通过塑炼机的机械挤压和摩擦力的作用使长链橡胶分子降解变短由高弹性状态转变为可塑状态。热塑炼是向生胶中通入灼热的压缩空气在热和氧的作用下使长链分子降解变短从而获得可塑性。氯丁橡胶也能耐某些酸碱,使用温度80℃;丁腈橡胶耐油,可用至80℃。市场橡胶产品橡胶橡胶护弦厂家
橡塑作为保温材料,由于材料的特性决定了它的使用优势。专注橡胶产品医用橡胶管
硅橡胶 汽车发动机硅橡胶密封制品的使用寿命可满足10年以上及15万公里的苛刻要求。近年来,无需二次硫化的硅橡胶新品种已研制成功。用纳米稀土元素氧化物配制的耐高温硅橡胶应用研究获得突破,使硅橡胶耐热温度提高了50℃,并改善了硅橡胶的粘接性和机械强度。 硅橡胶应用於密封制品的领域相当大,主要制品有汽车发动机曲轴後密封圈、燃油泵密封件、空调压缩机密封件、TPV挤出发泡电位器绝缘衬套和灌封材料等。PV挤出发泡就是用合成橡胶制成的密封条,又称为防护性成型镶条。主要应用在车门门框、侧面车窗、前后档风玻璃、发动机盖和行李箱盖上,起到密封的作用,另外也起到减振保护的作用。专注橡胶产品医用橡胶管
上海西郊橡胶制品厂专注技术创新和产品研发,发展规模团队不断壮大。公司目前拥有较多的高技术人才,以不断增强企业重点竞争力,加快企业技术创新,实现稳健生产经营。诚实、守信是对企业的经营要求,也是我们做人的基本准则。公司致力于打造高品质的橡塑制品,橡胶制品,橡塑密封解决方案,橡胶密封圈。公司凭着雄厚的技术力量、饱满的工作态度、扎实的工作作风、良好的职业道德,树立了良好的橡塑制品,橡胶制品,橡塑密封解决方案,橡胶密封圈形象,赢得了社会各界的信任和认可。
上一篇: 工业橡胶产品宜春橡胶地板
下一篇: 规模橡胶产品地板橡胶垫