宁波FMEDA潜在故障
ISA-84.01还开创了“安全生命周期”的概念,这是一个系统的设计过程,从概念过程设计开始,到SIS退役结束。安全生命周期图的简化版本如图1-2所示。ISA-84.01-1996标准已被更新的ANSI/ISA-84.00.01-2004(IEC61511Mod)[6]所取代。该标准几乎与全球使用的IEC61511[7]标准逐字逐句地相同,除了为涵盖现有安装而添加的条款。该标准是涵盖各行各业的国际功能安全标准系列的一部分。整个系列标准基于IEC61508[8]标准,该标准是非行业特定的,可用作整个系列的参考或“伞状”标准。许多人认为这一系列标准对可靠性工程领域的影响超过任何其他标准。FMEDA可以帮助制造商遵守相关的法规和标准,满足客户和监管机构的要求。宁波FMEDA潜在故障
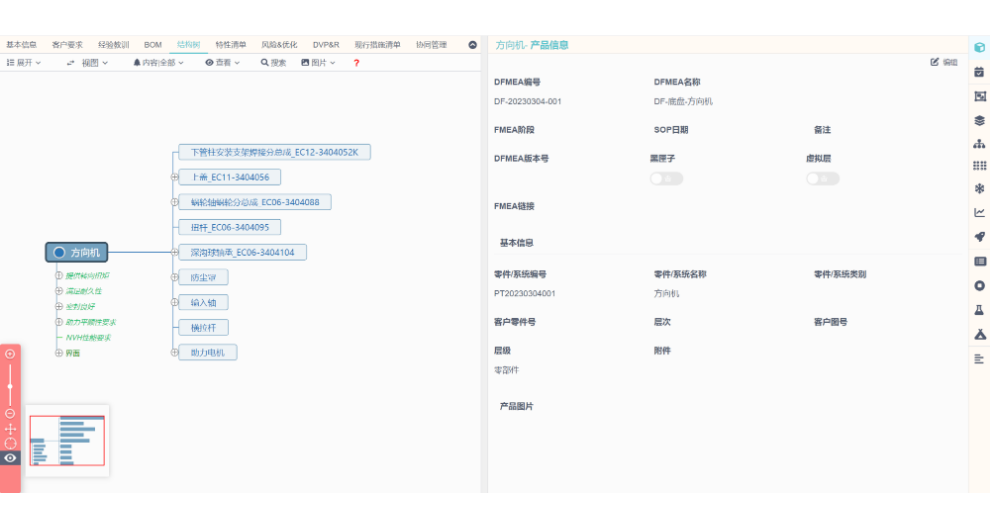
立片:立片主要发生在小的矩形片式元件(如贴片电阻、电容)回流焊接过程中。引起这种现象的主要原因是元件两端受热不均匀,焊膏熔化有先后所致。失效后果:导致开路,引发电路故障,会使系统或整机丧失主要功能,严重度评定为7e现有故障检测方法:人工目视检测。失效原因分别为:贴片精度不够,频度为3,检测难度为5,其风险指数PRN为IOS.回流焊接预热温度较低,预热时间较短,频度为5,检测难度为4,其风险指数PRN为140。现行控制措施:适当提高预热温度,延长预热时间。焊膏印刷过厚,频度为5,检测难度为5,其风险指数PRN为1750现行控制措施:针对不同的器件选用适当厚度的丝印模板。在计算了各潜在失效模式的RPN值之后,后续工作就是开展相应的工艺试验,探寻针对高RPN值和高严重度的潜在失效模式的纠正措施,并在纠正后,重新进行其风险评估,验证纠正措施的可行性与正确性。宁波FMEDA潜在故障FMEDA可以应用于电子元器件、系统和软件等方面的可靠性分析。
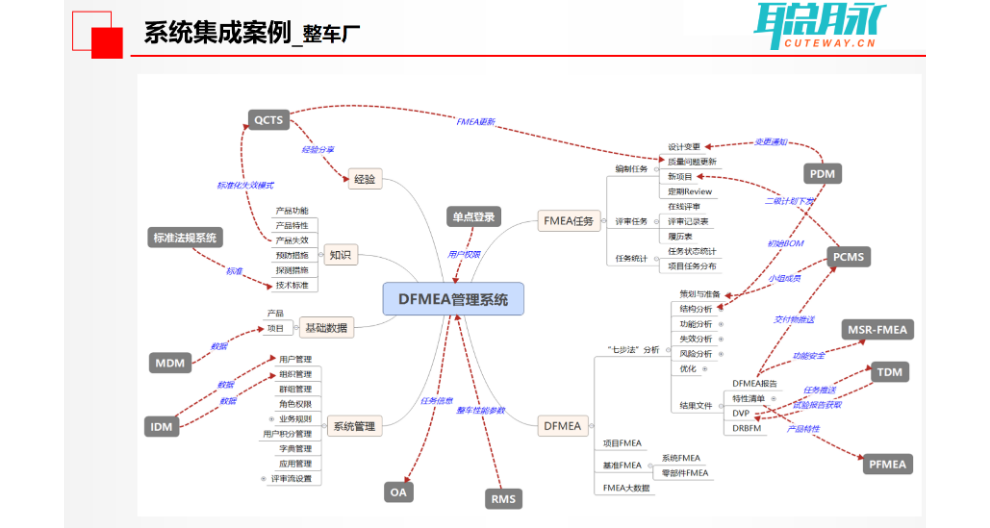
在IEC61508中,使用FMEDA要完成两个安全完整性等级的测量;即:危险非检出型失效率和众所周知的安全失效分数,即SFF。SFF表示不危险和能检出的失效百分比。然而,这个对于系统级模型非常重要的定量型数据,也可以从同一个FMEDA容易地导出,这比IEC61508起初的方法更有效,FMEDA驱使流程的进一步进化,并且提高了其结果的价值。IEC61508标准的未来草稿更新工作正在进行,会做进一步的改进。IEC61508失效模式定义:IEC61508部分(1998年)定义一个危险失效是一种失效,"有可能把安全相关系统推向危险或者不能工作的状态"。这个标准还定义一个安全失效也是一种失效,"无可能把安全相关系统推向危险或者不能工作的状态"。
灯灭了是功能丧失,只有一盏灯亮,有一盏灯不亮,那是部分功能,性能损失。灯点亮200小时后,亮度下降,那是功能退化,灯太亮,那是过度功能,超出预期。灯在点亮时发热,发热是不期望的要求,那是非预期的功能,安全气囊在20ms内点爆,那是功能延迟。机油泵的泄压阀的功能:当油压大于9Bar时,泄压至油压小于2Bar,泄压时间小于20ms。功能丧失,如:在油压大于9Bar时,无法泄压;部分功能,如:在油压大于9Bar时,泄压后的油压大于2Bar;功能退化,如:无(由于功能中没有涉及到可靠性的要求)。FMEDA可以帮助制造商制定有效的测试计划和维修策略,提高元器件的可靠性和安全性。
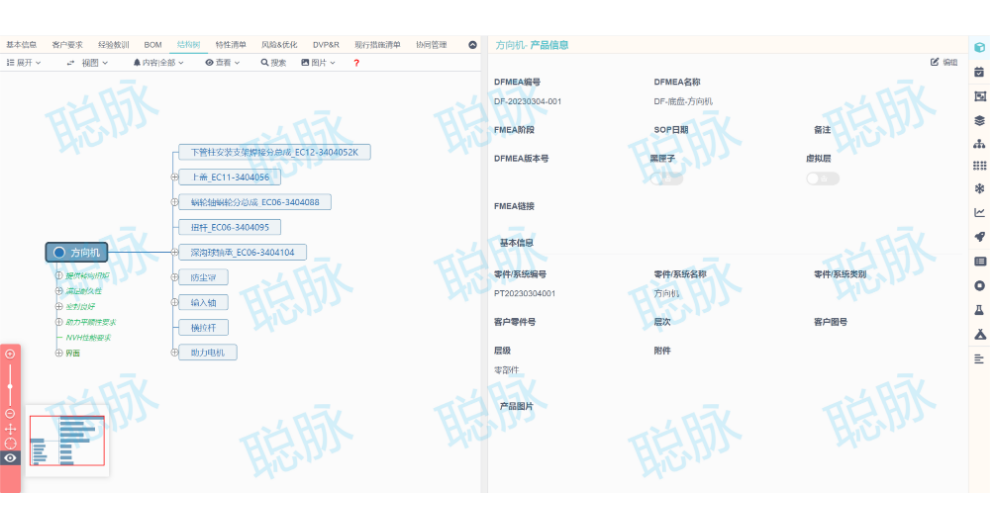
使用者PFMEA“失效后果”:是指失效模式对产品质量和顾客可能引发的不良影响,根据顾客可能注意到或经历的情况来描述失效后果,对使用者来说,失效的后果应一律用产品或系统的性能来阐述,如噪声、异味、不起作用等;PFMEA使用者“现行控制方法”:是对当前使用的、尽可能阻止失效模式的发生或是探测出将发生的失效模式的控制方法的描述。这些控制方法可以是物理过程控制方法,如使用防错卡具,或者管理过程控制方法,如采用统计过程控制(SPC)技术。FMEDA需要考虑元器件的工作环境、应力水平、使用寿命等因素。宁波FMEDA潜在故障
FMEDA的分析需要考虑系统的故障模式和效应的可靠性保障方法,以便确定系统的可靠性水平。宁波FMEDA潜在故障
PFMEA包含哪些呢?频度(O):指某一特定的起因/机理发生的可能发生,描述出现的可能性的级别数具有相对意义,但不是一定的。探测度(D):指在零部件离开制造工序或装配之前,利用第二种现行过程控制方法找出失效起因/机理过程缺陷或后序发生的失效模式的可能性的评价指标;或者用第三种过程控制方法找出后序发生的失效模式的可能性的评价指标。其风险优先数(RPN):指严重度数(S)和频度数(O)及不易探测度数(D)三项数字之乘积。顾客:一般指“使用者”,但也可以是随后或下游的制造或装配工序,维修工序或有关部门的法规。宁波FMEDA潜在故障
上一篇: 嘉兴FMEDA问题假设
下一篇: 南昌FTA分析衍生