内蒙古设备完整性管理与预测性维修系统程序
设备完整性管理与预测性维修系统内置的检查提醒功能,有效减少了因人为疏漏导致的设备管理问题。传统的设备检查往往依赖人工记录和记忆,容易因遗漏或延迟而导致潜在隐患未能及时发现。系统通过设定周期性检查提醒,在检查到期前自动向管理人员发送通知,确保检查工作按计划实施。此外,系统还支持根据设备运行状态调整提醒周期,例如对于高负荷设备,可以设置更频繁的检查提醒,从而更好地保障设备的安全性。这一功能大幅度提升了设备管理工作的可靠性和效率。设备完整性管理与预测性维修系统支持企业用户实时查看设备的运行记录、保养历史和检查状态。内蒙古设备完整性管理与预测性维修系统程序
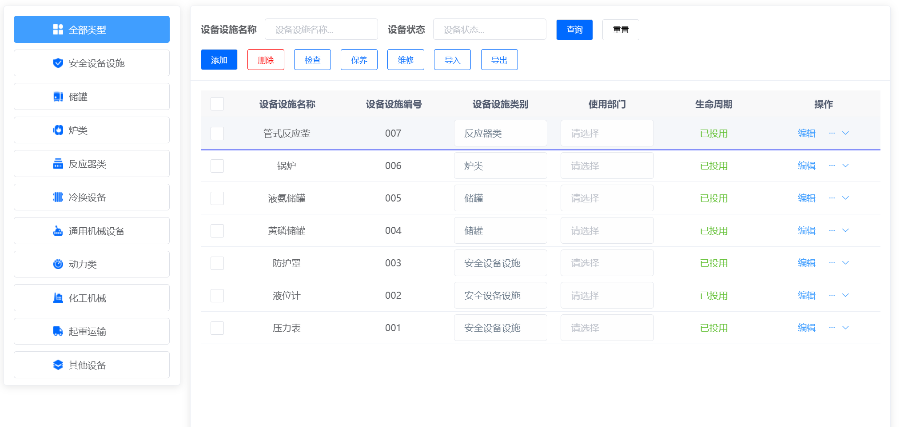
设备完整性管理与预测性维修系统配备了报警信息分级处理功能,为企业提供了更清晰的报警管理机制。系统可以根据报警的重要程度、涉及设备的关键性及潜在风险,自动对报警信息进行分级,例如分为高危、重要或一般等等级。对于高危报警,系统会优先推送给相关负责人,并启动应急响应流程;而对于一般报警,系统则建议定期检查,减少不必要的干扰。这种分级处理方式,有助于企业更高效地分配资源,集中精力解决重要问题,同时也提升了报警管理的条理性和针对性。通过这一功能,企业能够更加有序地应对复杂的设备管理需求,提升整体的运行效率和安全保障能力。内蒙古设备完整性管理与预测性维修系统程序设备完整性管理与预测性维修系统支持对设备设施的分类管理,方便用户快速筛选和查看重点设备的运行情况。
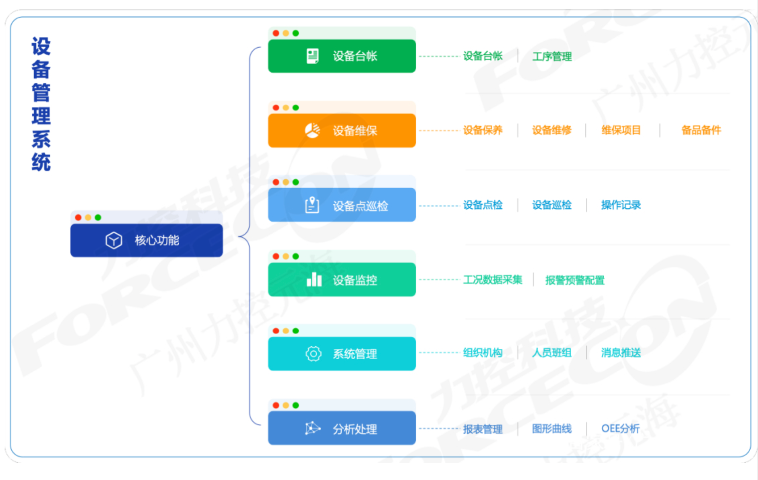
设备完整性管理与预测性维修系统通过设备分类管理功能,使企业能够更轻松地整理和查看不同设备的运行情况。针对企业复杂的设备结构,系统可根据设备类型、功能、重要性等级等参数建立清晰的分类体系。管理者可以快速筛选出需要重点关注的设备,如生产线上的主要设备或存在隐患风险的老旧装置。分类管理不仅提高了设备信息的查阅效率,还为后续的状态监控、数据分析及维修维护提供了坚实的基础。通过这一功能,企业可以避免遗漏关键设备的管理需求,提升了对设备运行情况的掌控能力,同时有效减少了因信息混乱导致的管理漏洞。分类管理的便捷性,使得设备完整性管理与预测性维修系统在大规模设备运行环境中成为不可或缺的管理工具。
检测指标灵活配置功能,是设备完整性管理与预测性维修系统的一大亮点。系统允许企业根据设备特性、运行环境及工艺需求,灵活设置检测指标及报警参数。例如,对于易燃易爆场所,企业可以为气体监测设备设定更低的报警阈值;而对于一般设备,则可以采用较宽松的检测范围。这种灵活的设置方式,确保了设备监测方案能够与实际需求紧密结合。更重要的是,系统支持根据季节变化或设备运行状态,动态调整检测指标。例如,冬季时为防止低温冻裂,可设置管道温度的下限报警;而在设备老化时,可增加振动和噪音检测参数,以发现潜在故障。这种灵活配置不仅减少了误报率,还让管理人员能够更高效地识别真正的风险,集中资源进行维护和整改,从而提升了整体的设备运行效率。设备完整性管理与预测性维修系统帮助企业在设备管理中实现了标准化流程,减少了因管理不善导致的安全隐患。
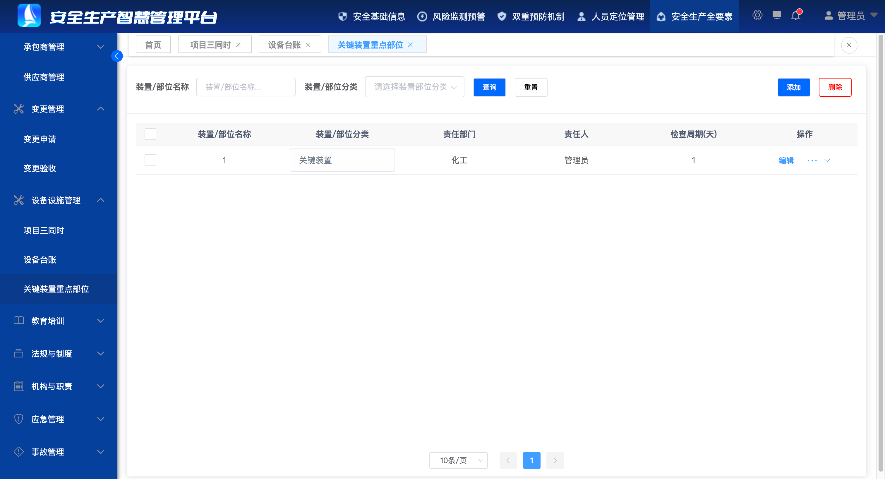
设备完整性管理与预测性维修系统整合了设备监测、报警、维修记录、趋势分析等多项功能,为企业打造了一站式的设备管理平台。无论是检查计划的制定、故障信息的跟踪,还是设备状态的实时查看,所有操作都可以在一个界面中完成。这种整合式的管理方式不仅提升了工作效率,还降低了多系统切换带来的时间浪费。同时,系统支持多用户协同操作,为企业的设备管理团队提供了统一的工作平台。通过这一平台,企业可以实现设备管理的数字化和智能化。设备完整性管理与预测性维修系统帮助企业通过预警机制,避免因设备突发故障导致的生产中断。企业设备完整性管理与预测性维修系统售后服务
设备完整性管理与预测性维修系统将重点设备的检查检测指标集成到统一的平台,提升了设备维护的精确性。内蒙古设备完整性管理与预测性维修系统程序
设备完整性管理与预测性维修系统通过对安全管理责任制的支持,帮助企业有效落实各级管理职责。系统允许企业为每台设备分配具体的责任人,并记录检查、维护和故障处理的全过程。例如,当某设备发生异常报警时,系统会自动将信息发送给责任人,并记录其处理情况及反馈意见。这种明确责任分工的方式,不仅提高了设备管理的效率,还强化了企业员工的安全意识。同时,系统生成的责任追踪记录,也为企业评估管理成效提供了重要参考。例如,对于管理到位的部门,可以进行表彰激励;而对于责任落实不到位的情况,则可以及时调整管理策略。通过这一功能,企业实现了从被动管理到主动监督的转变,进一步提升了设备的安全保障能力。内蒙古设备完整性管理与预测性维修系统程序
上一篇: 上海设备完整性管理与预测性维修系统简介
下一篇: 天津提供设备完整性管理与预测性维修系统