油水分离机的原理
机床油水分离机的后期使用过程主要包括以下几个步骤:1、定期检查:在使用过程中,需要定期对机床油水分离机的各个部件进行检查和维护,包括沉淀池、油水分离器和纯水过滤器的清洁和保养等。2、排污清洁:在使用过程中,需要定期对沉淀池和油水分离器进行排污清洁,以去除沉积在底部的杂质和污垢。同时,需要定期清洗或更换油水分离器和纯水过滤器的滤材。3、更换耗材:在使用过程中,需要定期更换纯水过滤器的滤芯等耗材,以保证出水水质和设备的正常运行。4、监测水质:在使用过程中,需要对出水水质进行监测,以保证水质符合要求。一般而言,机床油水分离机处理后的水质可以达到工业用水的标准。机床油水分离机的人性化设计使得操作和维护更加简单方便,按键控制使得操作更加直观。油水分离机的原理
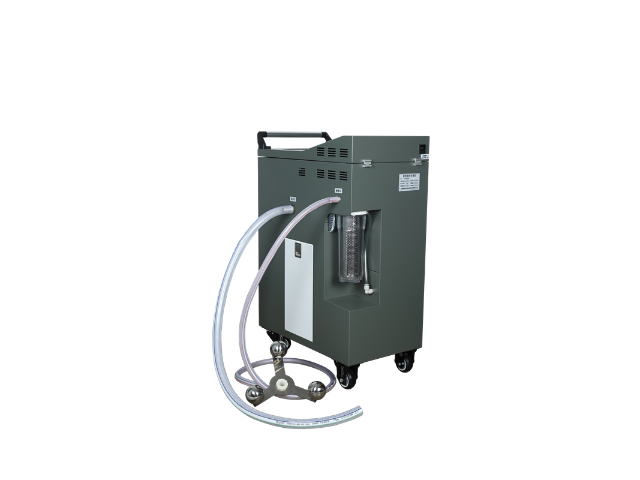
机床油水分离机的油盒内置液位传感器和保护开关,当油满时,液位传感器会发出信号,保护开关会自动断开电源,防止设备因油满而发生故障。同时,设备还具有提走储油盒自动停机的功能,确保了设备的安全运行。机床油水分离机具有智能报警功能,当设备出现异常情况时,如油满、电机过热等,设备会自动发出报警信号,提醒用户及时处理。此外,设备还具有远程监控功能,用户可以通过手机APP或电脑端实时查看设备的运行状态,了解设备的工作情况。机床油水分离机采用先进的分离技术,可以将油水混合物中的油和水分离开来,实现资源的再利用。同时,设备在运行过程中无需添加任何化学物质,对环境无污染。合肥小型油水分离机价格机床油水分离机的价格合理,性价比高,值得广大用户选择。
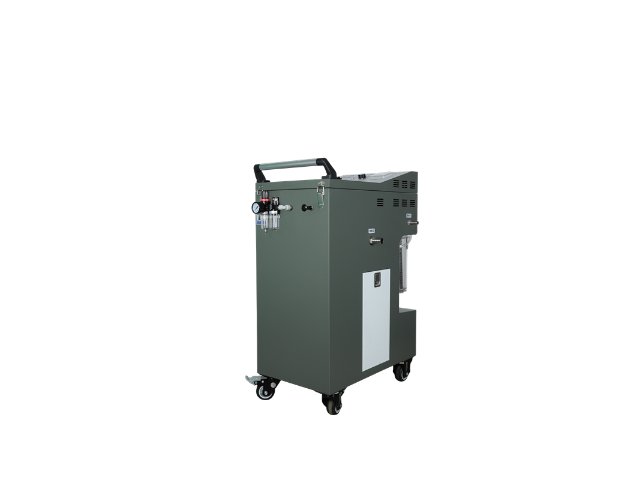
机床油水分离机通常采用三级过滤装置,分别是沉淀池、油水分离器和纯水过滤器。沉淀池是机床油水分离机的一级过滤装置,主要作用是去除切削液中的大颗粒杂质和悬浮物。沉淀池通常采用自然沉淀的方式,将切削液中的杂质沉在池底,通过底部排污阀排出。油水分离器是机床油水分离机的第二级过滤装置,主要作用是利用物理原理将切削液中的油和水进行初步分离。在油水分离器中,切削液会通过一定的流速和角度进入分离室,通过自然浮力原理,将油和水初步分离。同时,一些细小的油滴也会被吸附在内部滤材上,通过定期清洗或更换滤材,可以保证油水分离器的分离效果。纯水过滤器是机床油水分离机的第三级过滤装置,主要作用是采用精细过滤技术,将水中残留的油滴、悬浮物和微生物等杂质过滤掉,从而得到纯净的水。纯水过滤器通常采用不锈钢滤网、滤芯等高精度过滤材料,可以有效地去除水中的微小杂质,保证出水水质。
随着工业自动化水平的不断提高,机床油水分离机在各个行业的应用越来越普遍,随着环保政策的不断加强,对切削液的处理要求也越来越高。因此,机床油水分离机市场需求将持续增长:1.技术创新:随着科技的不断进步,机床油水分离机的技术水平也在不断提高。未来的机床油水分离机将更加智能化、高效化、节能化,满足各行业对切削液处理的高要求。2.市场需求:随着工业自动化水平的不断提高,机床油水分离机在各个行业的应用越来越普遍。随着环保政策的不断加强,对切削液的处理要求也越来越高。因此,机床油水分离机市场需求将持续增长。在高效过滤和杀菌除臭的双重作用下,可以保证机床油水分离机的高效稳定运行,提高生产效率。
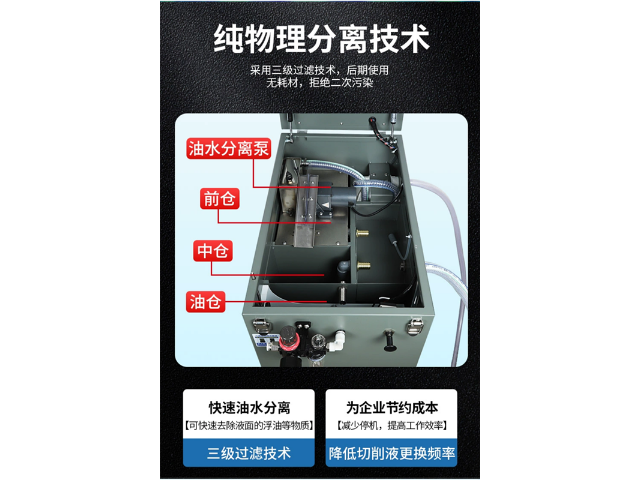
在传统的机床油水分离过程中,需要安排专人值守,定时检查设备的运行状态,及时清理油水混合物,这不仅增加了人工成本,还容易因为处理不及时而给生产带来负面影响。而新一代的机床油水分离机,通过智能化技术,实现了无需停机、无需人员值守的功能,一键开启智能净化分离。新一代机床油水分离机采用了先进的智能化技术,可以实现自动化控制和操作。在设备运行过程中,只需按下启动按钮,设备就可以自动进行油水分离。同时,该设备还配备了智能控制系统,可以实时监测设备的运行状态和各种参数,如温度、压力、流量等,一旦出现异常情况,设备会自动停机并发出报警信号,确保生产安全。机床油水分离机的节能环保设计能够降低能耗,减少对环境的影响。合肥小型油水分离机价格
机床油水分离机内置的油水比重控制系统能够将油和水自动分离。油水分离机的原理
机床油水分离机具有以下特点:1、高除油率:机床油水分离机的除油率高达98%以上,能够在短时间内将冷却液中的油污和杂质迅速分离,提高冷却液的净化程度。2、无级调速电机:机床油水分离机采用无级调速电机,可以根据实际情况调整刮油盘的转速,使分离效果更好。3、大直径刮油盘:机床油水分离机采用大直径刮油盘,能够高效刮除冷却液中的油污和杂质,提高分离效率。4、自动控制:机床油水分离机配备有自动控制系统,可以自动化控制分离过程,减少人工干预,提高生产效率。5、耐用性强:机床油水分离机的配件采用特殊材料制作,不易损耗,能够长时间使用,减少维修和更换配件的频率。油水分离机的原理
上一篇: 立式铣床维修费用标准
下一篇: 宁夏数控车床油水分离机器