广州制造企业生产管理系统
塑胶生产涉及到大量的原材料、能源和设备的使用,如何合理利用这些资源、减少浪费和排放是企业关注的重点。生产管理软件能够通过精细化的资源管理,帮助企业实现原材料的精确采购、库存的合理控制、设备的有效利用等,从而降低生产成本、提高资源利用效率。同时,软件还能够通过对生产过程的优化和控制,减少能源消耗和废弃物排放,实现节能减排的目标。生产管理软件在塑胶行业的应用具有诸多优势。首先,它能够提高生产效率和产品质量,增强企业的竞争力。其次,软件能够实现资源的合理配置和节能减排,降低生产成本、提升企业社会责任感。生产管理软件在模具行业的应用,为企业提供了强大的数据支持,助力企业科学决策和持续发展。广州制造企业生产管理系统
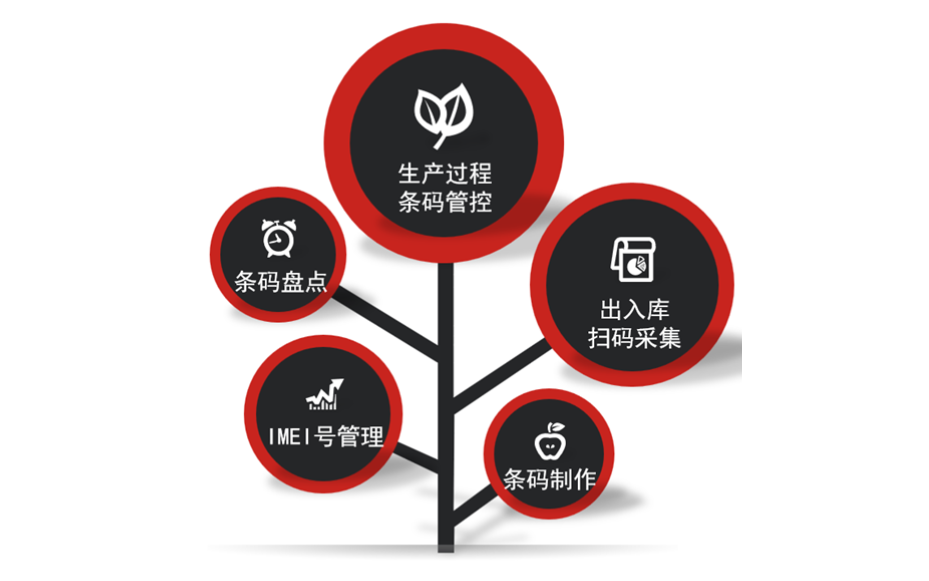
近年来,随着生产管理软件的不断完善和普及,越来越多的五金企业开始尝试引入生产管理软件来优化生产流程、提升管理水平。生产管理软件通过集成计划管理、生产调度、物料管理、质量管理等多个功能模块,实现了对生产全过程的实时监控和调度。在五金行业中,生产管理软件的应用主要体现在以下几个方面:1、生产计划管理:通过生产管理软件,企业可以根据市场需求和产能情况制定合理的生产计划,实现按需生产,避免库存积压和浪费。同时,软件还可以对生产进度进行实时监控,确保生产计划的顺利执行。2、物料管理:五金行业涉及的原材料种类繁多,库存管理难度较大。生产管理软件通过实现物料信息的实时更新和共享,帮助企业准确掌握库存情况,减少物料浪费和缺货现象。此外,软件还可以根据生产计划自动生成物料需求计划,实现物料的精确采购和库存管理。深圳定制生产管理软件生产管理软件提供实时的生产进度跟踪,帮助企业及时应对生产中的突发情况。
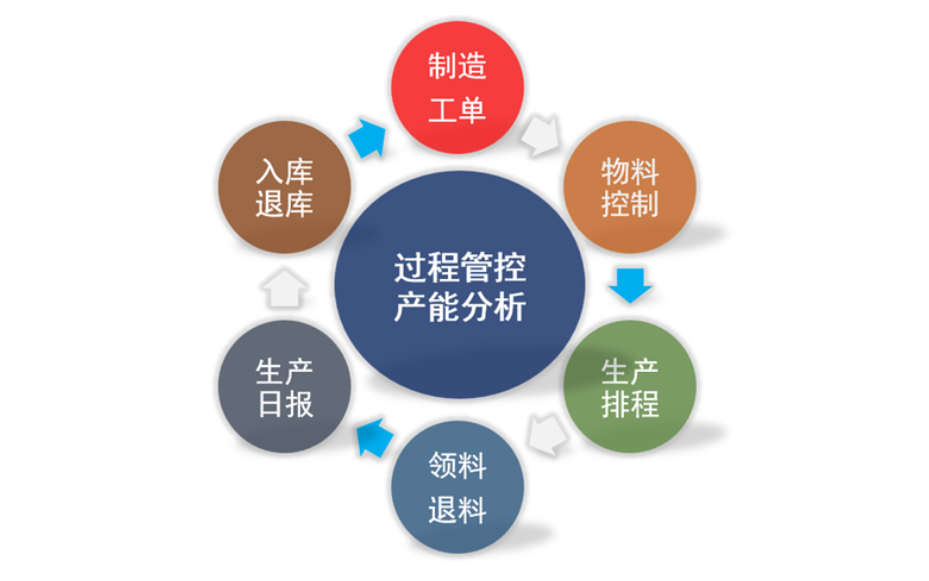
生产管理软件能够帮助模具企业实现生产计划与排程的优化,通过对订单、库存、生产能力等数据的分析,软件可以自动生成较优的生产计划和排程,确保生产任务的合理安排,避免生产过程中的瓶颈和浪费。同时,软件还能够实时监控生产进度,及时调整计划,提高生产效率。模具行业对产品质量的要求非常高,而生产管理软件可以帮助企业实现质量管理的提升。软件可以记录和分析生产过程中的各项数据,包括原材料的使用情况、生产设备的运行状态、产品的质检结果等,从而及时发现和解决质量问题。此外,软件还可以建立质量管理体系,规范生产流程,提高产品质量的稳定性和一致性。
生产管理软件能够实现生产流程的标准化与自动化,传统的生产管理模式往往存在信息传递滞后、人工操作误差等问题,而生产管理软件则通过数字化手段对整个生产流程进行统一规划与实时监控,从而确保每一个生产环节都能够按照既定标准执行。无论是物料采购、库存控制,还是生产计划、工艺路线设定,都可以借助软件实现精确调度与智能管理,有效降低了人为错误的发生概率,提高了生产效率和产品质量。生产管理软件有助于提升资源利用效率,通过实时收集并分析生产数据,软件能够精确预测物料需求,有效减少库存积压和过度采购,从而降低成本,提高资金周转率。同时,通过对设备运行状态的实时监控,可及时进行预防性维护,延长设备使用寿命,降低故障停机时间,进一步提升生产效能。通过生产管理软件,企业可以实时监控设备的运行状态,及时进行维护保养,延长设备使用寿命。
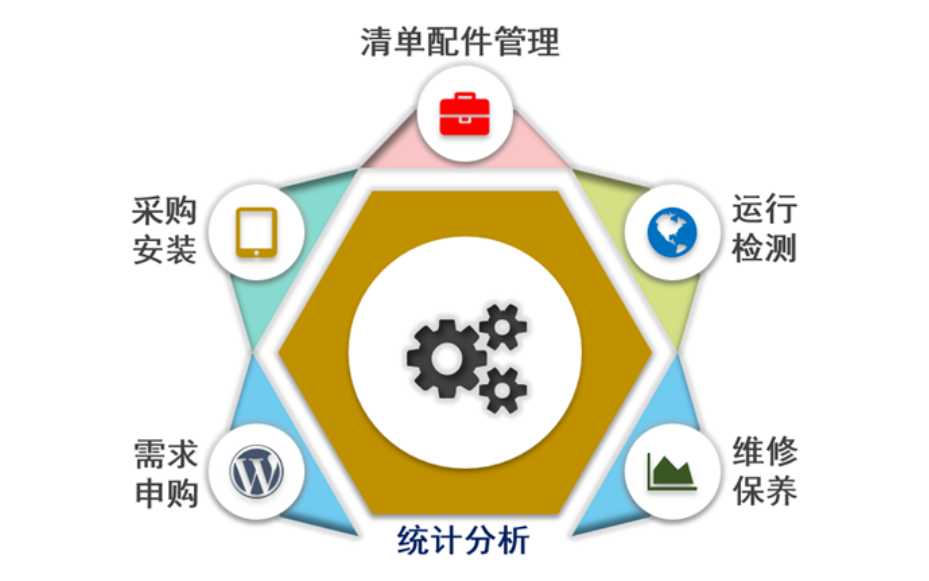
塑胶产品的质量直接关系到企业的声誉和客户的满意度,生产管理软件通过集成质量检测、质量追溯、统计分析等功能,实现对产品质量的控制。软件可以对生产过程中的关键环节进行监控,及时发现和纠正质量问题。同时,软件还可以记录产品的生产信息、检验信息、使用信息等,为产品的追溯和质量分析提供数据支持。生产管理软件通过收集和分析生产过程中的数据,为企业提供决策支持。软件可以生成各种报表和图表,展示生产进度、设备运行状态、产品质量等信息,帮助企业及时发现问题和改进管理。同时,软件还可以通过对历史数据的挖掘和分析,为企业制定生产计划和战略提供参考。通过生产管理软件,企业可以对员工绩效进行量化评估,激励员工提高工作效率。工厂生产管理的软件服务公司
模具行业生产管理系统支持在线协作功能,能够方便各部门之间的沟通和协作。广州制造企业生产管理系统
生产管理软件往往具备强大的协作功能,不同部门可以在统一平台上共享信息、协调工作。这种跨部门的沟通减少了信息孤岛现象,提高了团队的整体工作效率。如某化工企业通过实施管理软件,使得研发、生产、销售等部门实现了信息共享,有效缩短了产品开发周期。在当前快速变化的市场环境中,生产管理软件能够帮助企业快速适应市场变化,及时满足客户个性化需求。通过对市场动态的实时监控和分析,企业能够迅速调整生产策略,推出符合市场需求的新产品。就像服装行业一样,时尚潮流的变化要求企业必须具备快速反应能力,生产管理软件则提供了这样的可能。广州制造企业生产管理系统
上一篇: 标准化生产管理系统收费
下一篇: 安全生产管理软件系统服务费用