江苏真空热处理方法
大型锻件的锻后热处理通常是紧接在锻造过程完成之后进行的。其主要目的简述如下。(1)消除锻造应力,降低锻件的表面硬度,提高其切削加工性能。这是锻后热处理较直接和较初的目的。(2)对于不再进行较终热处理(或产品热处理)的工件,通过锻后热处理还应使锻件达到产品技术条件所要求的各种性能指标。这类工件大多属于碳钢或低合金钢制成的锻件。(3)调整与改善大型锻件在锻造过程中所形成的过热与粗大组织,降低大型锻件内部化学成分与金相组织的不均匀性,细化钢的奥氏体晶粒;提高锻件的超声波探伤准确性,消除草状波,使得锻件中的各种内部缺陷都能够较清晰地显示出来,以杜绝不合格锻件向下道工序的转移。SA508Gr3钢核电大型锻件锻压后经900~980℃正火,650~700℃回火处理,锻后热处理工艺曲线如下图所示,通过锻后热处理改善锻件内部组织及晶粒度,消除内应力,进一步降低氢的含量并使其尽可能均匀分布,为后续的性能热处理做好准备。淬火目的:提高硬度和耐磨性:刀具、量具、磨具。江苏真空热处理方法
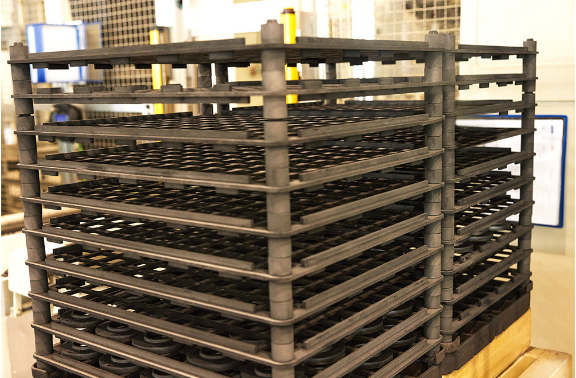
科技水平发展使得金属热处理技术也在不断提升,老的热处理方法都会对环境造成一定的污染,而且这会对人的身体健康构成威胁,现代科技对热处理技术进行改进,接下来爱力德热处理为大家分享当下绿色节能的热处理技术供大家使用。可控气氛热处理,可控气氛热处理主要是防氧化和脱碳,并对渗碳和渗氮做到精确的控制。20世纪80年代末开始应用于工业生产,发展到现在应用非常普遍。中外各设备厂家结合中国市场的特点全新推出各种档次、功能多样的可控气氛热处理炉。浙江金属热处理工艺回火获得所需要的力学性能。
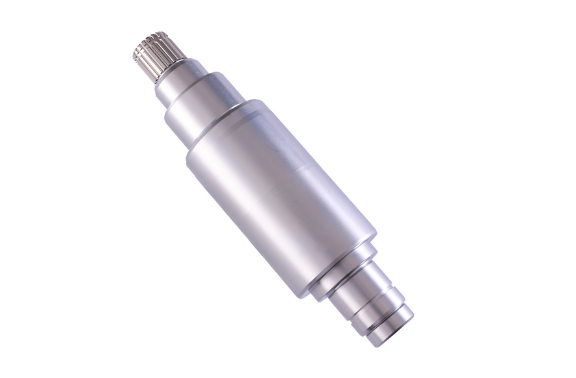
钢的退火,概念:将钢加热、保温后缓慢冷却,以获得接近于平衡组织的工艺过程。1、完全退火,工艺:加热Ac3以上30-50℃→保温→随炉冷到500度以下→空冷室温。目的:细化晶粒,均匀组织 ,提高塑韧性,消除内应力,便于机械加工。2、等温退火,工艺:加热Ac3以上→保温→快冷至珠光体转变温度→等温停留→转变为P→出炉空冷;目的:同上。但时间短,易控制,脱氧、脱碳小。(适用于过冷A比较稳定的合金钢及大型碳钢件)。3、球化退火,概念:是使钢中的渗碳体球化的工艺过程。
正火:1、定义:将钢材或钢件加热到一定温度,保温适当时间,使之完全奥氏体化,然后在空气中冷却,以得到珠光体组织的热处理工艺。2、目的:改善切削性能,消除毛坯内应力,细化晶粒、提高硬度、获得比较均匀的组织和性能。退火和正火的区别:退火和正火属于预备热处理工艺,对于含碳量相同的工件,正火后的强度和硬度要高于的退火的。例如:含碳量大于0.5%的碳钢和合金钢,为降低硬度便于切削加工采用退火处理;含碳量低于0.5%的低碳钢和低合金钢,为避免硬度过低切削时粘刀,而采用正火适当提高硬度。一般用于锻件、铸件和焊接件。退火一般安排在毛坯制造之后,粗加工之前进行。对于某些高淬透性的钢,空冷即可淬火,如采用回火软化既能降低硬度,又能缩短软化周期。
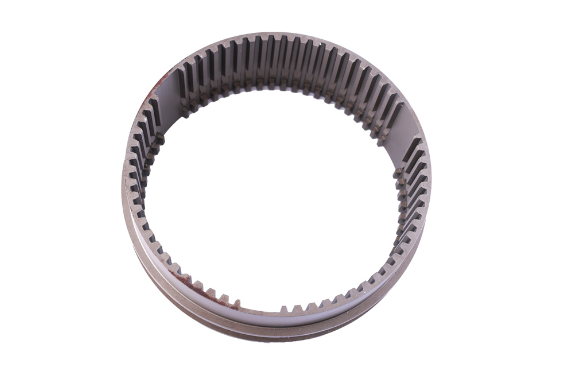
通常按加热温度的高低,回火可分为以下三类。(1)低温回火:加热温度为150℃~250℃。低温回火组织为回火马氏体,马氏体内析出碳化物形成回火马氏体,残余奥氏体也转变为回火马氏体。回火马氏体易受侵蚀,组织呈暗色针状。回火马氏体具有高的强度和硬度,而韧性和塑性较淬火马氏体有明显改善。其目的主要是降低淬火钢中的内应力,减少钢的脆性,同时保持钢的高硬度和耐磨性。常用于高碳钢制的切削工具、量具和滚动轴承件及渗碳处理后的零件等。(2)中温回火:加热温度为350℃~500℃。中温回火组织为回火屈氏体,它是由铁素体和粒状渗碳体组成的极细密混合物。回火屈氏体有较好的强度,较高的弹性,较好的韧性。其目的主要是获得高的弹性极限,同时有高的韧性。主要用于各种弹簧热处理。(3)高温回火:加热温度为500℃~650℃。高温回火组织的回火索氏体,它是由粒状渗碳体和等轴形铁素体组成混合物。回火索氏体具有强度、韧性和塑性较好的综合机械性能。其目的主要是获得既有一定的强度、硬度,又有良好的冲击韧性的综合机械性能。将加热后的不锈钢圆棒迅速冷却,通常采用水冷淬火。上海化学热处理厂家
将不锈钢圆棒加热到预定的温度,这个温度取决于所需的较终性能。江苏真空热处理方法
回火:高温回火所得组织为回火索氏体。回火一般不单独使用,在零件淬火处理后进行回火,主要目的是消除淬火应力,得到要求的组织,回火根据回火温度的不同分为低温、中温和高温回火。分别得到回火马氏体、屈氏体和索氏体。其中淬火后进行高温回火相结合的热处理称为调质处理,其目的是获得强度,硬度和塑性,韧性都较好的综合机械性能。因此,普遍用于汽车,拖拉机,机床等的重要结构零件,如连杆,螺栓,齿轮及轴类。回火后硬度一般为HB200-330。江苏真空热处理方法
上一篇: 安徽钢铁热处理方法
下一篇: 上海钨钢低压渗碳过程